Japan
サイト内の現在位置を表示しています。
画像処理コントローラへのディープラーニング活用による外観検査ソリューション
デジタルトランスフォーメーションを加速するAI活用サービス・ソリューション工場系のサービス・ソリューションとして、不良品検出の共創事例を紹介します。検査領域へのAI活用が注目されるなか、ラインセンサーシステム専業メーカーと共創し、画像検査検品システムの中核となる画像処理ソフトにNECの「RAPID機械学習」を組み込んだソリューションを構築しました。機械学習を組み込んだ画像検品システムを容易に構築できる顧客価値に加え、NECの技術を共創パートナーの製品に組み込むことにより、新たな領域への展開、ものづくり現場のデジタル化への貢献を目指します。
1. はじめに
日本の高品質なものづくりは、熟練検査員の目視による全数検査による品質保証で支えられてきました。近年、検査員の高齢化による退職や、一層の人員効率化要求が加速するなかで、人的リソースに依存した品質保証体制の維持が困難となってきました。これに伴って、昨今、製造業の外観検査システムへのディープラーニングを中心としたAI技術の適用が進んでいます。
しかし、画像撮影(撮像)と画像の処理、また画像分析を一連のソリューションとして扱うことには課題がありました。撮像と分析を同時に行うソリューションがなく、それぞれの工程で処理を行い、更に結果に結び付ける処理が追加で必要となっていたからです。今回、日本エレクトロセンサリデバイス株式会社殿(以下、NED社)の持つ「TechView」と、NECのディープラーニングソフトウェアである「NEC Advanced Analytics - RAPID機械学習 画像解析版」(以下、RAPID機械学習)の共創により、前述の課題を解決するソリューションを実現することができました。
従来、NED社は画像撮影、またその画像処理に強みを持っており、NECはディープラーニングによる分析に強みを持っていました。今回双方の技術を融合したことで、検査検品領域での適用範囲を拡大することが可能になります。「TechView」は簡易にアプリケーションを構築でき、さまざまなデバイスと連携可能です。また、「RAPID機械学習」は、従来のルールベースの画像解析技術では実装が困難であった「外観検査における曖昧な判定基準」を、画像から自ら学ぶことで実現できます。双方のシステムをシームレスに連携することで、マシンビジョンとディープラーニングによる検査システムを簡単に構築できると同時に、「TechView」の持つ画像処理ライブラリーを活用することで「RAPID機械学習」に必要な「良質な教師画像」の自動収集が可能になります。また、オンプレミスでのシステム構築が可能なため、検査データを外部に保管したくないユーザーのニーズに応えることもできます。
本稿では、第2章において「TechView」の製品/撮像の概要について説明し、第3章において「RAPID機械学習」の概要について述べます。続いて第4章において、2つの製品を組み合わせた効果、ユースケースについて述べ、最後に今後の展望を記載し、まとめます。
2. 「TechView」と撮像システム
「TechView」とは、NED社が開発した、画像処理ライブラリーを搭載しているハードウェア一体型のコントローラです。画像処理に必要なさまざまなデバイスやツールと連携することが可能であり、画像処理を基本とした多くの外観検査システムで活用されています。外観検査システムは主に工場において検査員が目視で検査していたところをシステム化することにより、検査業務の省人化と品質基準の均一化を実現させるものですが(図1)、その大きな導入課題として次のことが挙げられています。検査対象の撮像のためのカメラや照明機器の制御、画像処理だけでなくAIも活用した画像検査、検査結果を表示・確認できる検査画面、検査後の各種制御機器との連携、という一連のシステム構築(図2)に対してプログラム開発などのリソースを割くことが困難という点です。更に、検査対象の撮像においては欠陥の特徴をとらえた画像の撮像が難しいという点もあります。次に、これらの課題を解決する方法を紹介します。
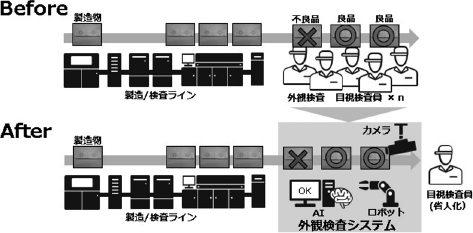
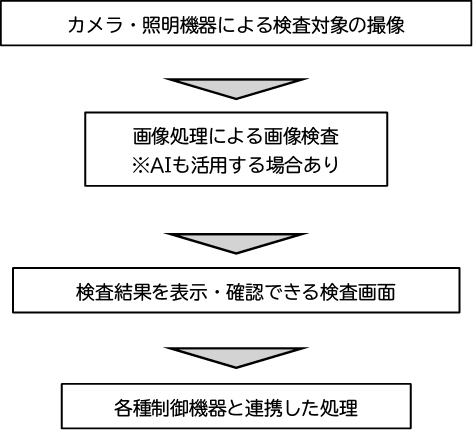
2.1 「TechView」の特徴
「TechView」の外観は図3のようになっており、さまざまなインタフェースが搭載されています。
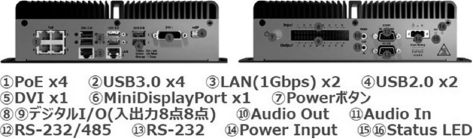
その特徴としては、次の2点が挙げられます。第一の特徴は、カスタムによる画像処理開発と比べて、プログラミングスキルが不要でフローチャートによる容易な処理設計が可能という点です。また画像処理ライブラリーが搭載されているため、パターンマッチングや画像加工(二値化、切出し、輝度調整)など、さまざまな処理を実現させることができます。第二の特徴は、カメラや照明機器、ロボットや制御機器、更にAIなど、画像処理に必要なさまざまなデバイスやツールと連携することが可能である点です(図4)。
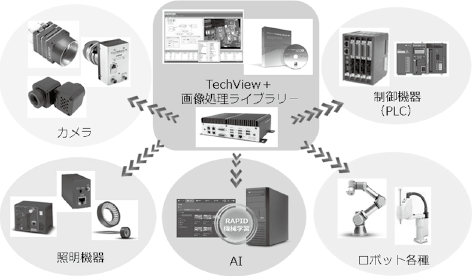
前述の特徴から「TechView」を活用することにより、図2で示した一連のシステム構築をプログラム開発することなく実施することができます。
2.2 撮像システム
カメラ・照明機器による検査対象の撮像においては、欠陥の特徴をとらえた画像をどういう機器でどのように撮るかといったことを考慮する必要があります(図5)。
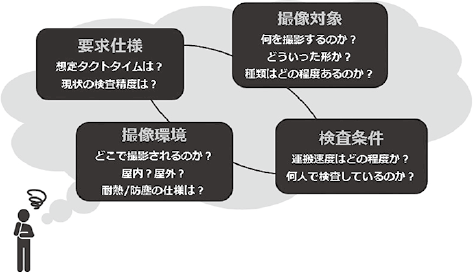
例えば、継続して移動する検査対象を切れ目なく撮像できるラインスキャンカメラの場合、検査対象の欠陥の特徴をとらえることができる分解能を持っているか、ということが選定ポイントになります。その際、検査対象の幅方向(X軸)と移動方向(Y軸)の考慮が必要になります。幅方向は検査対象を含めた視野から算出し、移動方向は検査対象の移動速度とカメラの最短スキャン周期から算出することができます1)。
NECは、40年以上にわたり産業用ラインスキャンカメラを市場に提供しているNED社と連携して、ラインスキャンカメラだけでなくエリアカメラや赤外線カメラなども含めて欠陥視認性の高い画像取得に最適な撮像システムの構築をサポートしています。
3. 「RAPID機械学習 画像解析版」
「RAPID機械学習」は、直感的に操作可能なGUIを備え、非専門家であっても簡単にディープラーニングを用いた画像認識アプリケーションを開発できるソフトウェアです。「RAPID機械学習」は、画像解析による外観検査自働化の実績を多数保有し、製造現場の目視による品質保証工程の省力化・省人化に貢献しています。
昨今、外観検査システムにディープラーニングを導入する課題として、次の2点が注目されています。第一の課題は、歩留まりの高い製造ラインで、ディープラーニングが良品・不良品の特徴を学習するための不良品画像を準備できない点です。第二の課題は、一般にディープラーニングは判定理由や根拠を提示しないため、ユーザーが認識精度を改善するために施策立案することが困難という点です。次に、これらの課題を解決する技術を紹介します。
3.1 ワンクラス分類
第一の課題を解決するワンクラス分類は、良品の画像のみを学習して、良品との「違い」を定量化することで不良品を摘出する技術です(図6上)。従来、良品画像間の共通的な特徴が複雑なケースでは、良品を不良品と誤判定する過検知が発生する問題がありました。本技術では、NEC独自の手法によって、例えば良品の表面模様がランダムなケースでも、過検知を効果的に抑制できます。
不良品の画像を1枚も必要とせずに、判定モデルを作成することができるという点が高く評価されています。
3.2 転移学習
第一の課題を解決する転移学習は、少量の教師画像を準備するだけで、高精度な画像認識を可能とする技術です(図6下)。本技術では、「RAPID機械学習」があらかじめ用意している一般物体を分類可能なモデルに対して、解きたい課題(メタル部品のキズ検知など)の少量データを追加学習させることで、その課題に特化した新たなモデルを作成できます。
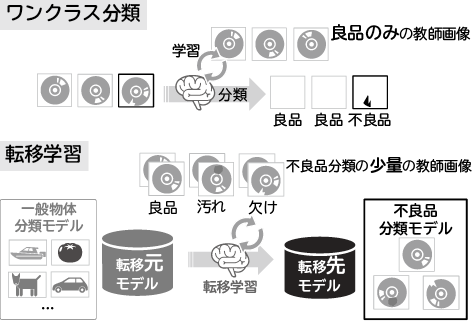
3.3 誤判定根拠可視化技術
第二の課題を解決する誤判定根拠可視化技術は、ディープラーニングの判定根拠をユーザーが理解できるように見える化する技術であり、「RAPID機械学習」への搭載を検討中の先進技術です(図7)。本技術は、誤判定した画像に対して、「モデルの注視度を示すヒートマップ」を出力します。ユーザーは、ヒートマップで可視化した誤判定の根拠を確認しながら、モデルのブラッシュアップに向けた施策を立案できます。例えば、誤判定した画像に対して、モデルが背景を注視して判断していることが分かれば、「背景のバリエーションを増やした教師画像を追加することで、精度が改善するのではないか」という仮説を立てることができます。
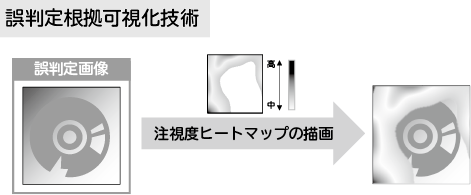
4. 「TechView」と「RAPID機械学習」の組み合わせ
「TechView」のフローチャートでは「RAPID機械学習」による判定処理も設定することができるため、通常の画像処理だけでは判定困難な官能系の検査項目についても「RAPID機械学習」のワンクラス分類機能など高度なAIアルゴリズムを容易に利用することができます。
図8は、異物検知の場合のフローチャート例になります。通常の画像処理だけでは判定困難な場合のみ、事前に学習済みのAIモデルによる判定を実施させるようなフローチャートを作成することにより、判定処理を効率的に実行させることが可能になります。また簡易的な検査画面表示であればフローチャートで設定できるので、AIも活用した外観検査システム構築をプログラム開発することなく実現することができます。
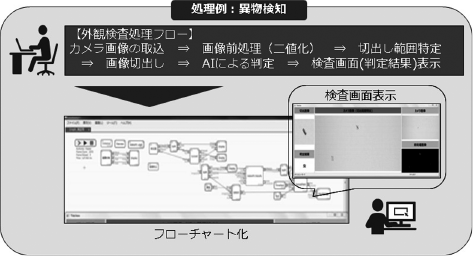
実際に工場ラインへ導入いただいている事例でも、「TechView」と「RAPID機械学習」を組み合わせることでマシンスペックを抑えつつ高精度かつ高速な判定処理を実施しています。
5. 今後の展望
本稿で解説した検査工程の自働化は、工場全体のデジタル化の流れにおける重要な要素の1つに位置付けられます。「TechView」と「RAPID機械学習」による検査工程の自働化の価値は、検査員・工数の削減だけではなく、検査員の習熟度に依らない検査品質の均一化を実現できます。更に、検査結果と製造工程の部品のトレーサビリティを組み合わせれば、どの工程で問題が起こったか素早く特定することが可能となります2)。また、検査結果と設備データや人作業データとの相関を分析することで、歩留まりの改善やコスト削減への貢献が期待できます。
今後のものづくりでは、サプライチェーン全体のデジタル化による、スループット向上と品質管理強化がますます重要となっていきます。NECでは、デジタルトランスフォーメーションが変えるものづくりの未来のコンセプト「NEC DX Factory」を提案しています(写真)。設計~製造~出荷~物流までのすべてのプロセスにおいて、人・モノ・設備をデジタル化しシミュレーション結果をフィジカルにフィードバックすることで、人と協調しながらロボット・生産設備の自律制御を行い、ものづくりの革新を実現します。先端技術を活用することで、多様化する顧客課題に対応するさまざまなソリューションを開発し、ものづくり現場へのデジタル化の導入とその価値提供を推進していきます。
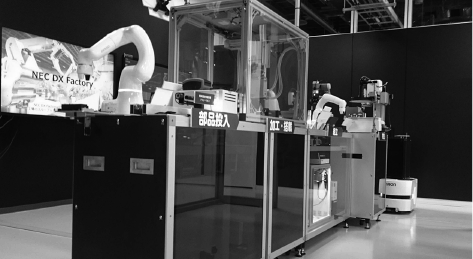
参考文献
- 1)今井 信司:産業用カメラの選び方・使い方,ラインスキャンカメラ,画像ラボ別冊,2018.4
- 2)
執筆者プロフィール
AIプラットフォーム事業部
マネージャー
AI・アナリティクス事業部
スマートインダストリー本部
マネージャー
スマートインダストリー本部
組込みビジネス営業本部
主任
プラットフォームソリューション事業部
マネージャー