Japan
サイト内の現在位置
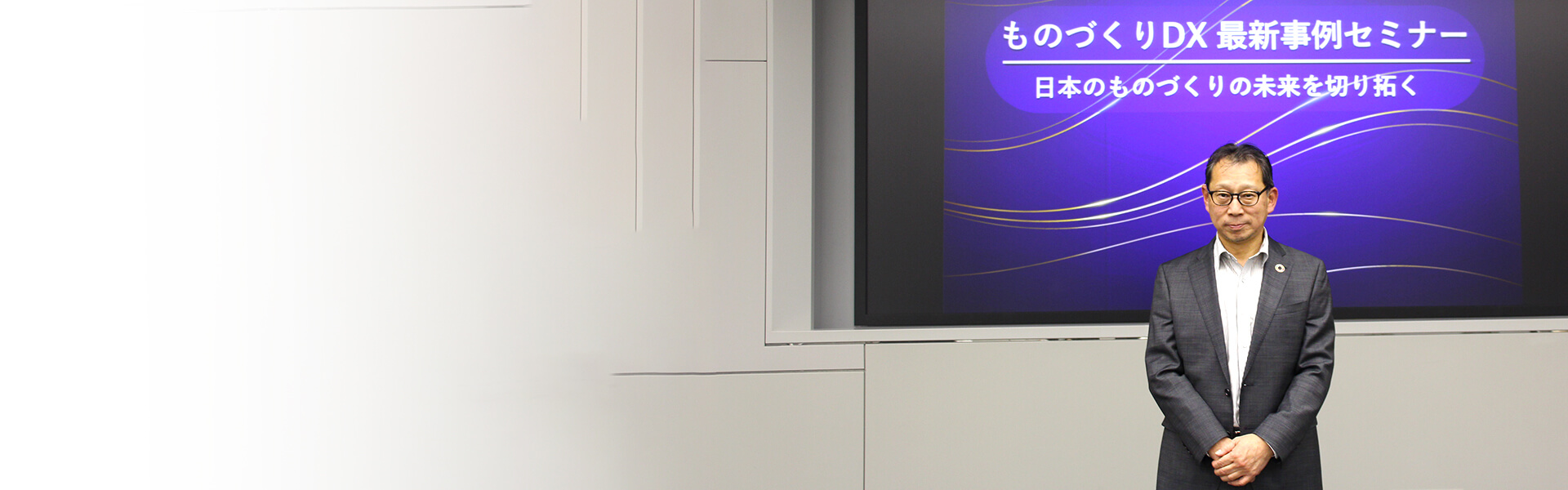
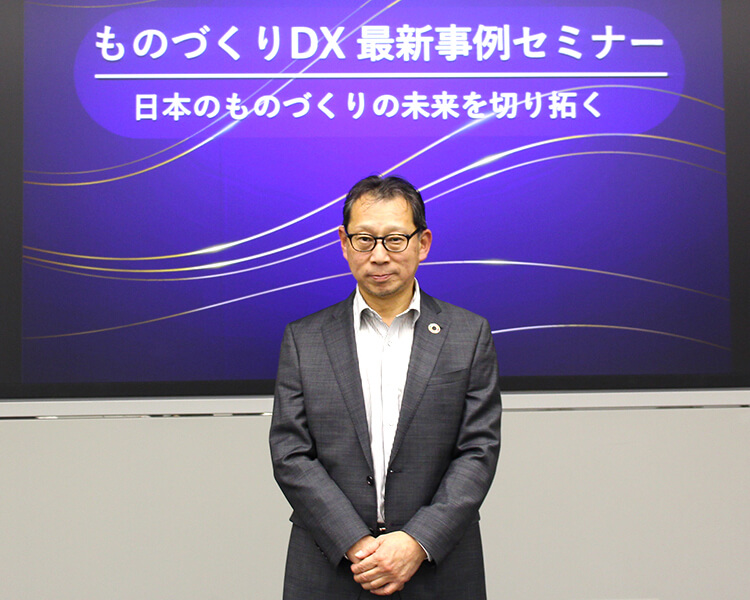
NECプラットフォームズの「ものづくりDX」に向けた取り組み
ものづくりDX最新事例セミナーレポート【2024.04.17】
カテゴリ:DX・業務改革推進生産技術・製造スマートファクトリー(IoT基盤/AI)
2024年2月21日、NEC本社で開催した「ものづくりDX最新事例セミナー」の特別事例講演として、NECプラットフォームズから「ものづくりDX」への取り組みやDX化を加速させる勘所について、20年に渡るものづくり革新の軌跡と活動の壁、それをどう乗り越えてきたのか、データドリブンを加速度的に推し進めるポイントなど、講演しました。その講演の内容についてご紹介します。
NECプラットフォームズ 執行役員 河野 修久
【目次】
NECプラットフォームズの概要と役割
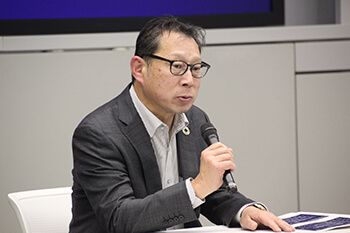
NECプラットフォームズは、NEC製品の設計・開発・製造を担当している売上高約3,600億円、従業員数約7,000名の会社です。
NECグループとして日本各地に開発生産子会社を設置し、さらに事業の統廃合を経て現在に至っています。
様々な製品を扱っているということもあり、異なる強みや特徴のある工場群が集まっていますが、全拠点共通で生産に必要な基盤を横軸機能として確定させながら、各領域の強みを伸ばしていっています。現在は「Together with “MONOZUKURI”, creating a sustainable society」をテーマに、「ものづくり」「コトづくり」を進化させ、持続可能な社会の実現を目指す中計目標「VISION 2025」に取り組んでいます。
NECグループのものづくり革新のあゆみ
NECグループが属する電機・電子機器業界では、古くは垂直統合の中で部品から製品までをお届けしてきましたが、90年代初頭から状況が大きく変わり、水平分業となり、ものづくりのスタイルを変えていく必要が生じました。そこでNECグループではものづくりのやり方を根本から見直す生産革新の取り組みに着手してきました。
生産ラインでは、ムダ取りや流れづくり、精度向上、標準化などに取り組んできました。例えば、様々な変化に追従していくために、従来の大きな設備への投資を見直し、もっと現場で使いやすいものにするため内製化に取り組みました。また近年では、データ利活用による効率化にも取り組んでいます。
NECの製品群は、宇宙から海底までの非常に幅広い社会インフラ領域を担っていますが、部品の共通化や生産の効率化は非常に重要です。そこで、開発においても、部品の標準化や、営業企画や設計などの上流からのフロントローディングとして後戻りのないプロセスをしっかり進めていく取り組みを進めています。
サプライチェーンの領域においては、全国物流網の構築やかんばん方式での調達運用、BTO(受注生産)やパートナー製品と共にご提供するクロスドッキングといった出荷方式も運用しています。
これらの活動を支える人財育成にも注力しています。特に工場の人財育成は難しいですが、机上だけでなく実際の生産現場を事例にした改善活動を通じて育成しようと、NECグループのメンバーが集まって自主研究会を発足させ、既に230回を超える活動を行ってきています。
「グローバルOne Factory」で目指すものづくりの姿とは
NECプラットフォームズでは、開発生産機能を結集し社会価値を創造するベースとして「グローバルOne Factory」化に取り組んでいます。国内海外各工場・拠点によって業態や物が違っていても生産に必要な共通基盤が存在することに着眼し、情報システムや生産技術、自働化の考え方や進め方を、拠点関係なく統一基盤という形で開発・運用することを進めています。国内14の開発・生産拠点、17の営業拠点、国内外5社の子会社が、各拠点の特長もしっかり伸ばしつつ、これらを横軸機能として全拠点を貫き、あたかも一つの工場として振る舞う「グローバルOne Factory」の取り組みを進めています。
「グローバルOne Factory」の取り組みの背景は何だったのか。大地震やCOVID-19のパンデミックなど、非常に大きな外的要因変化や、人口減少の中で労働力をどう確保していくかという悩ましい問題に、コストダウンと合わせて取り組まなければなりませんでした。また、お客様の様々なニーズ変化に応えていくためには、製造品種を増やしたり、状況によっては生産方法を変えなければいけません。さらに需要の変化もあり、多様な変化が複合的に発生し、落ち着いてものづくりをすることが非常にやりにくくなっていました。
このように複雑化した多様な要求に応えるために、リソースをどう確保していくかが生産現場として取り組まなければならない課題でした。そこで、我々は自社が保有するデジタル技術を最大限活用し、情報を活かしたものづくりに転換していこうという取り組みをこの10年ほど進めてきました。
生産現場だけでなく営業や開発、保守業務においても、モノや人が動くことで色々なデータが発生します。従来は属人化、あるいは紙の情報だったため共有が困難でしたがこれをデータに置き換え、一元管理し分析することで改善にしっかり活かしていきます。これらを工場ごとに行い、さらに工場間でやり取りすることにより、A工場で起こった事例をB工場でも活かす事ができるようになります。これを続けることで繋がっている数だけ事例も増え、ノウハウがたまっていきます。従来サイロ化していた拠点ごとの情報を一元管理することによってナレッジを増やし、より早く正確な判断に繋げていくことを目指しています。
また、関連するサプライヤーやパートナーとの繋がり、開発部門との連携もしっかり行っていく必要がありますがデータをどんどん活用していく上では、セキュリティをケアしなければなりません。またデータ通信については、無線の活用で多様な変化にも耐えうるような環境を構築していく必要があります。そこで我々は、データを扱うためのネットワーク環境をしっかり守るべく「セキュア生産」と名付けた管理体制を構築しています。
「データドリブン経営」を目指す ものづくりの将来像
また、これらを実現する上では、生産基盤を見直す必要がありました。NECグループではNECのサプライチェーン(SC)基盤/エンジニアリングチェーン(EC)基盤を強化していくと同時に、DX・GX(生産データ)基盤を導入することで、ものづくりにおける経営をデータドリブンで進めていくことにしました。
中心にはCADやPDMといった設計ツールを含むEC基盤があり、お客様からの所要情報を元にMRPを回したりSCMの情報を管理するSC基盤があります。さらに、製造現場からの情報とMES、生産管理の情報をものづくりDX・GX基盤で管理し、ものづくりに活用して行きます。さらにはお客様へ出荷後の保守サービスや廃棄も合わせてデータ化することによってお客様に最適な商品・サービスをご提供できる環境を構築していきたいと考えています。
特に工場内においては、これまでも部分的にサイロ化したデータで多様な事象のデータ解析を行い、実証してきましたが、手応えが得られつつもデータを繋がないとこれを活かせない状況に直面しました。そこで、これらを支えるものづくり基盤を導入しどんどん増えていくものづくりにおけるデータを集め、最大限活用していく方向に大きく舵を切りました。
また、セキュリティ強化の必要性から、生産用ネットワーク設備の一新や管理体制を変更し、セキュリティを担保できるセキュア生産システムの開発など、安全な環境の中で生産を遂行しています。
これを人体に例え、ものづくり基盤は脳、生産ネットワークは情報を運ぶ血管、セキュア生産システムは外からの刺激を防ぐ衣服というふうに捉え、頭と血管、衣服を工場に着せて生産を強化していくというイメージで進めています。
「NEC Industrial IoT Platform」の採用
ものづくりのデータ基盤に「NEC Industrial IoT Platform」を採用しました。従来はそれぞれの工場が独自にデータベースサーバを構築して賄ってきましたが、サイロ化する状態ではデータの利活用が横に広がらないという課題を強く感じていたのです。そこで、検討の結果、全社統一基盤づくりのためにNECの商用基盤を導入することでこれらの問題を解決しようと決めました。
いろいろなデータを集めてくる上で非常に大きなデータ基盤が必要になるわけですが、この「NEC Industrial IoT Platform」はそれに十分耐えられること、また我々の保有するAIも容易に実装できるということが評価のポイントとなりました。さらに、独自にスクラッチ開発したものだと、新しい機能を実装するにはデータの構造から見直さなければならないなど保守や更新に多大な手間を要しますが、商用基盤であればこうした手間をかけず、常に最新の技術環境を利用し続けることができると判断しました。
また、生産ネットワークについても、(1)不正な侵入を許さない、(2)侵入されても被害を拡大させない、(3)その状態を専門家によって監視するという3つのポイントでセキュリティ強化を進めています。
「データドリブン経営」への移行と取り組み事例
では、デジタル化により工場はどう変わるのか。従来は、人の経験値や紙の情報をベースに、時間をかけて熟慮した上で、いろいろな判断や意思決定を行ってきましたが今はもうそれではとてもスピード的に対応できない状況にきていると認識しています。
そこで、いろいろなデータを経営幹部と共有し判断できる環境をつくることで、意思決定を早めるということを実際に日々行っています。例えば、経営に必要な情報、開発の責任者が必要な情報を工場から発信し、共有しながらこれらを経営判断に使い始めており、これを「データドリブン経営」と呼んでいます。
従来、データドリブンでのQC活動として、個別にシステムを開発しデータをどう使えば効果が出せるのかという取り組みを行った事例があります。
IE(Industrial Engineering)手法に則り、現場で人の動きや物の動きを計測し、そのデータをまとめて分析し判断していましたが、こうした方法では数週間から1カ月がすぐに経ってしまい、PDCAサイクルは正しくても、変化に追従できないという課題がありました。
現在ではこのデータ収集および分析をシステムに任せることで、PDCAサイクルを高速に回せるようになりました。従来1カ月に1回程度だった改善サイクルを、2週間に1回、さらに週2回と短縮化し、現在では日々のPDCAサイクルが回せるところまで来ています。こうなると、データを使ってきちんとQCDの改善ができ、それが計数効果にも表れてきます。
他にも、非常に特殊な無線製品の場合、出荷時の判定だけでは読み切れないという状況がありました。従来は計測値から専門のエンジニアが色々なことを読み取ってきましたが、データ解析ができるメンバーがデータを分析することで、熟練ノウハウを保有する技術者と変わらない判定結果が出せるところまで追い込むことができています。
このように、各所で属人的だったプロセスが、データを用いた判断ができるようになったということから、データをたくさん集めて横に並べて見ていくことが非常に重要であると気づき、データ基盤の導入に踏み切りました。
また、生産計画の最適化が属人化することにお悩みになっている方もいらっしゃるかもしれません。これについてはNECで保有している量子アニーリング技術活用し、最適な順序立て計算をシステムの中で行うことで、従来は限られた職人でないと組めなかったスケジュールを、1日に何回でも見直しができるようになりました。
最近は、部品の納入遅延の問題で、生産計画を立てた途端急きょ変えなければいけないといった事態も頻繁に起こっていると思います。立ててしまった計画で無理やり進めて部品が足りず生産数がショートするといった事態を防ぐ上でも、生産計画が瞬時に回せることは工場にとって大きな強みになると捉え、目下適用しているところです。
また、省人化のための自動化では、例えば、それほどスキルを必要としない構内運搬は、自動化必須として、従来からAGVを活用していました。しかし、AGVだと部品をラインに供給するところの活用止まりで、完成した製品を出荷に持っていくところでは使えず人力でやっていました。これを、AMRの活用でラインの動きに合わせ自働搬送を実現しています。これには、「NEC マルチロボットコントローラ」というソリューションや弊社開発のローカル5G技術を活用し、構内搬送の無人化を実現しました。
外観検査においても同様で、人が判断するところを画像処理で効率化する事例は数多く出ていますが、例えば、コンベアに物が載った状況は撮像環境として悪く、よく撮れないなど、精度を上げるのが難しいといった悩みもあると思います。そこはロボットを活用し、ラインで流せないような製品も撮像し、機械学習を活用した画像判定を行うことで効率化を進めています。特に外観検査では、生産ラインのスタッフが正しく行っていることを証明するエビデンスとして、後からの検証も非常に楽になるという効用もあります。
さらに、人の動作そのもののデジタル化によって、動作の繰り返し性の確認を行ったり、工程の抜け漏れのアラートを上げるような仕組みが可能となり、こうしたデジタルを活用した人の動きのデータ化の強化にも取り組んでいるところです。
終わりに
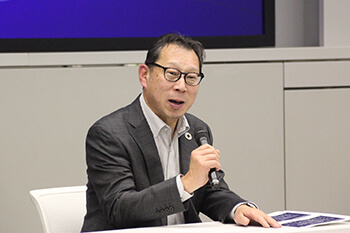
色々な工場の集合体だったため、データの利活用にあたっては、当初は工場間に壁がありました。これに対しては組織の見直しも行いました。具体的には生産技術・生産管理機能を拠点・部門を越えた大きな横軸組織とし、悩みやうまくやっていることを共有することで独自のこだわりを持ちつつも、重要・必要なことを学ぶ目線を育ててきました。また、工場ごとにばらばらだったERP・MES・PDMの仕組みを全社で統一・標準化したことで共通言語を生み、横断での会話がしやすくなりました。
データ利活用の取り組みには早い段階から内製で進めてきていましたが、これを加速していくにあたっては、強い意志が必要です。データを活用することで人のノウハウに匹敵する成果を得られるという手ごたえを得られたことからこの活動は加速して広がったと感じています。
また、大型投資は難しいので知見のあるメンバーで手製ツールで分析・現場へのフィードバックするところから始めましたが、規模を広げていくにはメンテナンスに手間がかかり、また新機能実装にはデータ構造の修正も必要となります。限られた自分たちのリソースを効率的に使うために、「餅は餅屋に」依頼し、商用基盤である「NEC Industrial IoT Platform」の活用に踏み切りました。これにより、最新サービスが安定的に提供されるのも重要なポイントだと考えています。
今後の更なる労働人口減少に対応するには、自分たちのリソースは事例を創出するところに使い、横に広げるには世の中にあるものをうまく活用することが大事です。
これまでご紹介してきた当社の活動が、お客様の安心安全、高効率、高品質なものづくりのご参考になれば幸いです。
関連リンク
ものづくりDX基盤「NEC Industrial IoT Platform」
設備、人(音声、映像)といった現場データに加え、ERP、PLM、MESなどのデータも集約し、工場、会社を横断したものづくりデータの見える化、分析を実現するのが「NEC Industrial IoT Platform」です。これにより、お客様の工場/ライン視点での生産性向上、品質安定化、さらに全社視点での損益の向上に貢献します。
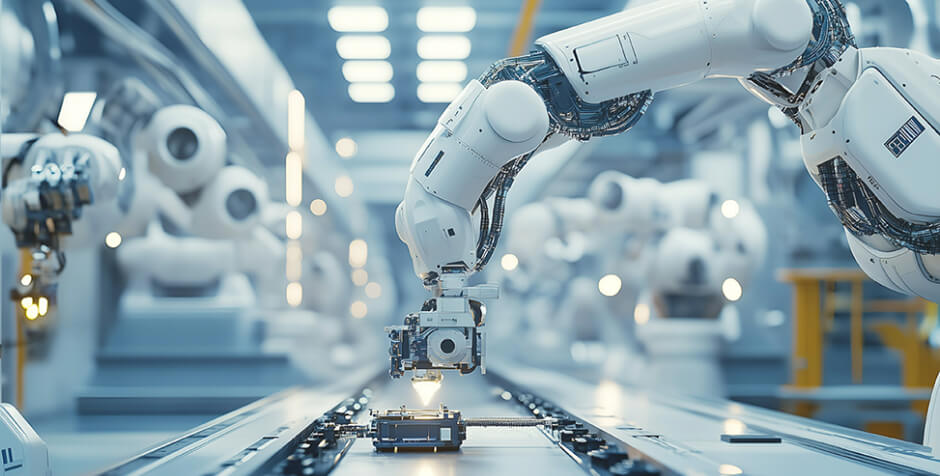
製造業向けソリューション
NECは、製造業である⾃⾝をゼロ番⽬のクライアントとして、AI/IoT などの最先端テクノロジーを⾃ら取り⼊れ実践し、その経験から得た製造業DXのノウハウをお客様に提供します。
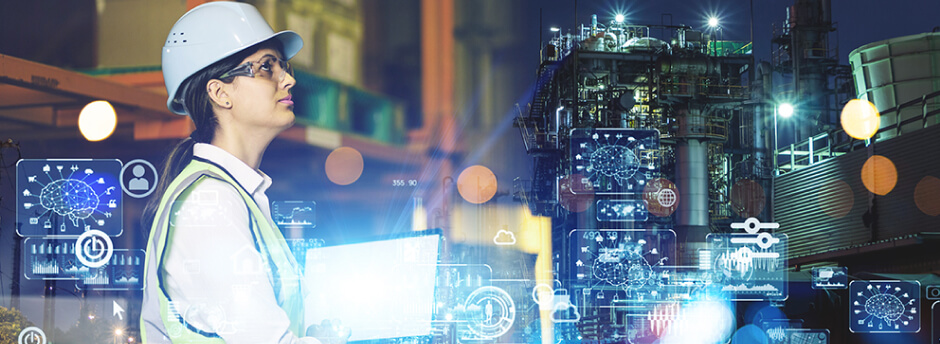
意味やメリット、実践方法を分かりやすく解説
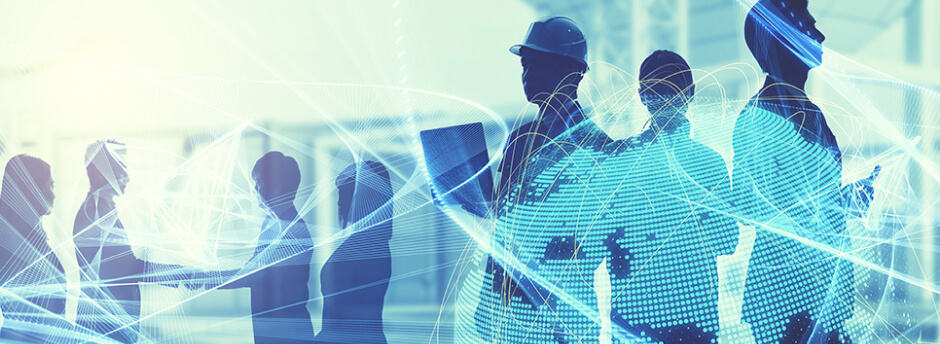
NECの革新ノウハウで業務改革や成長支援を包括的に実現
お問い合わせ