Japan
サイト内の現在位置
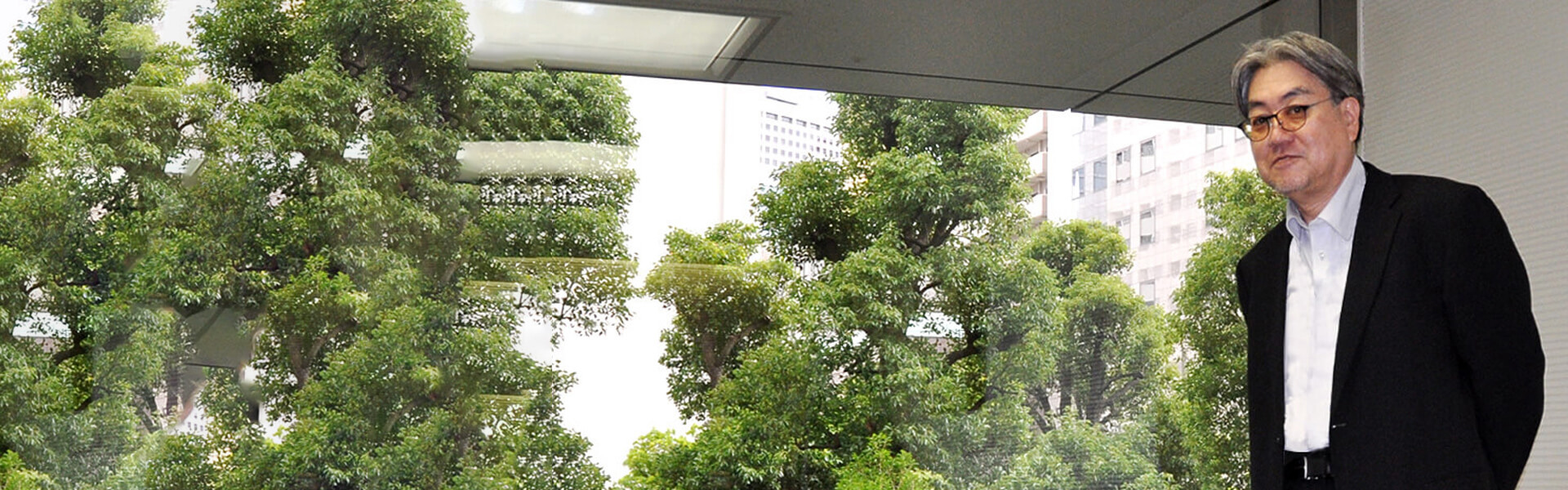
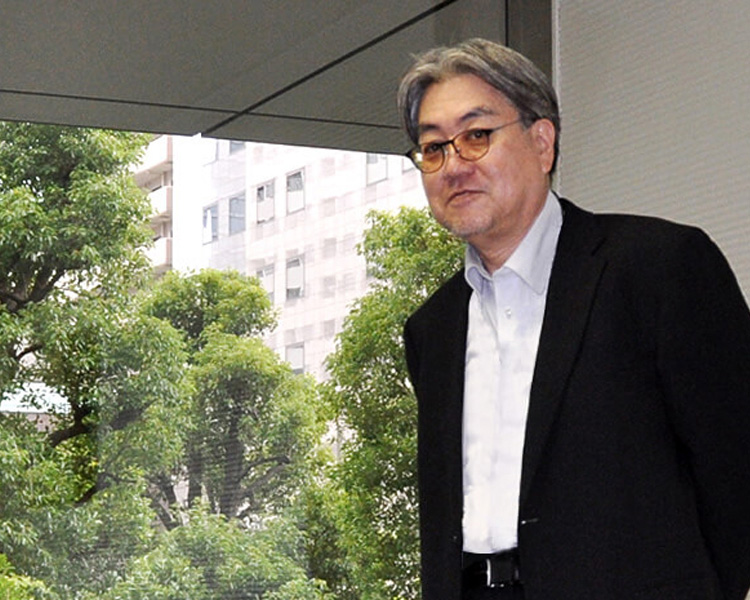
単純に人の作業を置き換えればいいのではない−ロボット導入成功の秘訣−
ロボット導入の匠インタビュー【2019.07.23】
カテゴリ:スマートファクトリー(IoT基盤/AI)その他
NECプラットフォームズ 生産技術統括部
エグゼクティブエキスパート 堀江寿身
NECグループ製品の開発・生産を担うNECプラットフォームズで生産技術の向上に取り組むスペシャリストとして、掛川事業所を皮切りに人協調型ロボットのライン導入を主導。その後全生産拠点への展開とともに、蓄積したノウハウをNECの「ロボット導入トータルサポートパッケージ」に結実させた。
NECプラットフォームズのロボット導入の背景
NECプラットフォームズは、NECグループにおける製品開発および生産を一体的に手掛けている企業として、生産性向上のために常に生産技術の改革・改善に取り組んでいます。
労働人口の減少や高齢化の中にあり、当社においてもさらなる業務効率化は待ったなしの課題となっています。そこで、2015年頃から登場した“人協調型ロボット”に着目し、現場作業員を補完する位置づけで生産ラインに導入する検討を始めました。
安全性が配慮された人協調型ロボットのメリットは、従来の安全柵に囲われた産業ロボットと違い、生産ラインの作業員と同じスペースに設置して稼働させることができること。これによって、労働人口が減っている日本のあらゆる製造業の課題解決の決め手となると期待されています。
確かに、ロボットは24時間365日、決められた作業を正確にやり続けることができるので、従来人がやっていた単純作業の生産性を劇的に向上させることが可能です。そこで、「ロボットを導入しさえすれば人手不足を解決できる」と受け止められるかもしれませんが、そんな単純な話ではないことが、自社への導入で明確となりました。
ロボット導入のプロセスとメリット・問題点
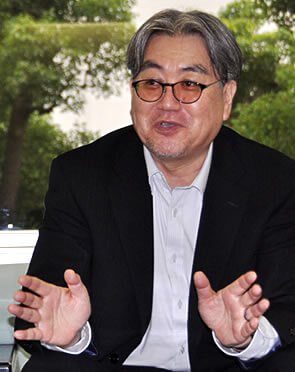
まず、人協調型ロボットの導入経験がなかったので、ロボットベンダーとコンタクトを取りつつ独自にリサーチを行いました。そして、第1号の導入先として掛川事業所のホームゲートウェイ(ルーター)製品の生産ラインが最適であろうと判断。その後、導入の試行錯誤を繰り返した結果、1年もの時間をかけて稼働しました。
同ラインは、①基板の製造、②製造した基板の検査、③部品に基板を組み込み製品化、という3工程に分かれます。その②および③の一部に作業員を補完する形でロボットを導入することにしました。
導入にあたっては、当該ラインの全動作要素を細かく分析し、ロボットが得意な「運ぶ」「セットする」といった動作を見極めた上で、ロボットに置き換えることが相応しい単純作業をピックアップしました。例えば、「グリスを塗る」という作業。人間だと塗る量や塗り方にバラつきが生じる上、人が作業を続けてくると疲れてくるので、作業が不安定となります。これをロボットに置き換えることで、バラつくことなく延々と作業させることができます。
しかし、実際にラインに導入してみると、事前に想定できなかったさまざまな問題が起こったのです。例えば、2つのロボットの可動範囲が干渉し合って稼働スピードが落ちたり、ロボットとコンベアの間隔や位置関係は把握できても、コンベアに乗せるパレットやその上の部品の位置のズレまでは把握できず掴み損なったり、といった問題が起こりました。人間ならば多少のズレは無関係にパッと掴むことができていたところです。そこで、このようなズレの最大公差時に正常に稼働するかを検証しようとしたのですが、要素があまりにも多過ぎました。そこで「まずやってみて、問題が起きたら解決策を考える」という方針を取り、できるだけ早いうちに失敗しそこから知見を得ることにしたのです。
ロボットの限界や弱点
また、ロボットにはいろいろな限界や弱点があることも見えてきました。例えば、ズレがあってもスムーズに掴むためにセンサーをつけて位置を補正できるようにすればいいと考えがちですが、その計算プロセスで動きが遅れてしまいます。また、ズレがあった場合などのサブルーチンをどこまで盛り込んでおくべきか、コストや時間との兼ね合いも考慮しなければなりません。結果的に、ズレへの対応が最小限になる基準点を見出すことで落ち着きましたが、ロボットにどこまでやらせるか、全体最適を考える必要があるといえます。
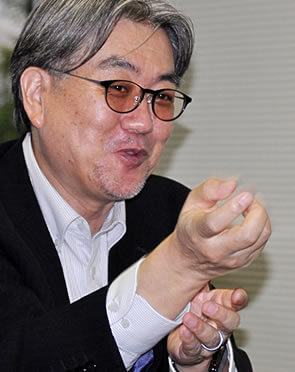
一方、ロボット特有の構造によるムダな動きにも注意が必要です。例えば、アームを回転させる場合、配線も巻き込む形となるため、回転を戻す必要が生じます。したがって、できるだけ回転数を減らすような軌道を設計する必要があります。人間の作業を1秒減らすよう突き詰める作業は、ロボットに対しても同様に必要なのです。さらに、同じ動きをし続けることで関節部などに負荷がかかり、ダメージを与えるという問題もありますので、経時的にロボットの“健康状態”をケアする必要性もあります。
試行錯誤の成果を「ロボット導入トータルサポートパッケージ」に結集
こうしたさまざまな試行錯誤を経て、掛川事業所から他の生産拠点に展開させ、全社的な生産性向上に繋げています。
一連の経験を通じて、ロボットの特性だけでなく、生産ライン全体の流れや人による作業を理解した上で、どの作業をロボットに任せるかを決める工程構想設計こそが非常に重要で、ここで成功するかどうかで8割がた決まってしまうと痛感しました。NECの強みは、ロボットSIだけでなく、この工程構想設計についての経験と知見があることと自負しています。
NECでは、こうした経験や知見をもとに、ロボット導入のノウハウを整理・体系化し、「ロボット導入トータルサポートパッケージ」として提供を開始しました。このパッケージには、ロボットのハードウェアだけでなく、関連する周辺装置や、ロボットを導入するためのコンサルティングサービス、人作業を含むライン設計、ロボットの稼働の見える化・分析を行うITサービスまでが包括されているので、生産性の高いロボットラインを短期間で立ち上げることが可能です。
デジタル・トランスフォーメーションを睨んだ今後の展開
今後は、デジタル・トランスフォーメーション(DX)を睨み、IoTやAIを積極的に取り入れ、ロボットだけでなく、設備や人作業、モノについてのデジタルデータを統合管理し、見える化・分析・対処して生産ライン全体のスループット向上と品質管理を強化することが製造業での生き残りのキーポイントになると思っています。
さらに、製造プロセス情報であるBOP(Bill of Process)と連携し、ロボット工程の最適設計をデジタルに行うことで、ロボット導入リードタイムの更なる短期化を目指していきます。
NECでは、ものづくりに携わるお客様と協働し、ノウハウを交換し合いながらソリューションを磨き上げる「NEC ものづくり共創プログラム」を運営していますが、こうした場も活用し、「ロボット導入トータルサポートパッケージ」を発展させ続けていきたいと考えています。
これからロボット導入をお考えの企業は、NEC DX Factory共創スペース(玉川事業場内)で「ロボット導入トータルサポートパッケージ」の実物展示を行っていますので、一度触れていただけるとイメージを掴んでいただけると思います。具体的なご要望があれば、お客様の生産ラインに対して最適なロボット導入を一緒に検討させていただくことも可能です。この機会にロボット導入への第一歩を踏み出してみてはいかがでしょうか。
お問い合わせ