Japan
サイト内の現在位置
三菱日立パワーシステムズ株式会社様


全部門・工程を横断したすべての生産関連情報を統合
現場情報を迅速に活かした新しいモノづくりを目指す
- 業種:
-
- 製造・プロセス
- 業務:
-
- 設計・開発・製造
- 生産管理
- 製品:
-
- ソフトウェア/情報管理
- ソフトウェア/その他
- ソリューション・サービス:
-
- 共通業務/ERP
- 共通業務/PLM
事例の概要
課題背景
- モノづくりの仕組みを標準化して生産性の向上を図りたい
- 各部門、プロセスに散在する生産管理情報を統合化したい
- 円滑なデータの連携と情報の整流化で生産計画の精度を高めたい
成果
工程間の連動による準備作業の実践
上流側での作業指導票の作成など、製造に先立つ準備作業を着実に実行できる体制が整った
担当者単位の作業工数が翌日には把握可能に
月末に作業チーム単位で集計・レポート化されていた作業工数が、翌日には担当者単位で把握できるようになった
過去の情報に基づく迅速な改善が可能に
IFS Applications上に蓄積された過去プロジェクトの情報をベースにプロセスの改善を迅速に行えるようになった
導入ソリューション


設計から生産計画や生産実績などの情報をタイムリーに一元管理できるシステムをObbligato ⅢとIFS Applicationsにより構築。設計から製造に至る一連のプロセス、および生産管理や調達、製造といった各部門間での円滑な情報連携により、生産にかかわるプロセスの標準化、標準時間を軸とした計画精度と生産性の向上を実現している。

本事例に関するお問い合わせはこちらから
事例の詳細
導入前の背景や課題

デジタルイノベーション統括部
ITソリューション部
長崎ITグループ
主席技師
今中 和久 氏
各部門、プロセスに散在する生産管理情報が大きな課題に
2014年2月に三菱重工業と日立製作所の火力発電システム事業が統合され誕生した三菱日立パワーシステムズ様。世界をリードするその高度な発電技術をベースに、大型火力プラントや主機の開発・設計・建設工事・試運転からアフターサービスに至るすべての工程をカバーできる世界でも有数の企業です。
ただし、グローバルレベルでの競争はさらに過酷さを増しています。欧米の有力企業が圧倒的なシェアを握る一方、新興国のメーカーの躍進にもめざましいものがあるからです。
「こうした厳しい環境の中で、当社がさらなる事業成長を図るには、統合前の両社が持っていた高品質な製品・サービス力を生かしながら、モノづくりを支える仕組みの標準化を図り、さらなる生産性の向上を目指していくことが不可欠です」と三菱日立パワーシステムズの今中 和久氏は語ります。

エンジニアリング本部
ボイラ製造統括部
生産技術部
戦略企画課
呉企画チーム
主席技師
池田 司 氏
そうした観点から同社の生産現場を見渡すと、いくつかの課題が存在しました。例えば、ボイラ製品の製造を担う呉、長崎の両工場では、設計から製造に至る一連のプロセス、あるいは生産管理や調達、製造といった各部門間の情報連携が必ずしも円滑になされていませんでした。
「もちろん、工数の見積もりや実作業工数といった個別の情報は、それぞれのシステムで管理されていました。しかし、別プロジェクトに関する予定・実績を把握しようとすると、各システムから必要なデータを収集し、加工・編集する必要があり、情報収集・加工に時間と煩雑な手間がかかっていました。そのような前捌き作業を削減し、本来行うべき判断を伴う業務に注力可能な環境を構築する必要がありました」と同社の池田 司氏は明かします。

エンジニアリング本部
ボイラ製造統括部
生産技術部
生産統括課
呉統括チーム
上席主任
上河内 功介 氏
「さらに、製造現場で工程計画を立てる際も、基本的には熟練者が、各プロセスに要する時間や人的リソースなどを、いわば“経験と勘”で判断し、策定している状況でした」と同社の上河内 功介氏は語ります。
選定のポイント

ボイラ技術本部
ボイラ製造総括部
生産技術部
戦略企画課
青田 洋子 氏
同じ製造業であるベンダーならではの的確な提案に大きな信頼感
こうした問題を解消するため、まず同社では呉工場のシステムの刷新に着手しました。その際、最も重要な要件となったのは、工場内の生産活動にかかわる、すべての部門・工程を横断したあらゆる生産関連情報が集約・管理できること。「すべての情報が集約・管理できれば、部門や工程をまたいだ円滑なデータ連携、情報の整流化はもちろん、生産にかかわるプロセスの標準化を図ることも可能になります。例えば、統合された情報を基に、工程の標準時間を策定。それを軸に計画精度や生産性を向上していくこともできるでしょう」と今中氏はその狙いを述べます。
こうして同社では新しいプラットフォームに関する検討を開始。そのシステム基盤として同工場が採用したのが、NECが提案したERP製品「IFS Applications」でした。
その理由について今中氏は次のように話します。
「IFS Applicationsは、先に挙げた当社の要件をトータルに満たしていました。加えて重要なポイントとなったのが、その高い柔軟性です。IFS Applicationsでは、我々の業態である個別受注生産、あるいは我々が採用する製番管理といった手法にも容易に対応可能です。当社が過去数十年にわたって築いてきたプロセスを変えることなく、IFSの標準機能を使いながらも独自のフロントエンド側の仕組みと連携できるIFSの柔軟性は、重要な評価ポイントとなりました」
パートナーとしてのNECに対する信頼感にも大きなものがありました。「長崎工場では、NECのPLM基盤である『Obbligato Ⅲ』を導入していましたが、その導入に際してもNECが非常に丁寧に支援してくれたことが印象に残っています。何よりも、同じ製造業であるという立場もあり、NECの提案内容は常に、メーカーとしての我々の課題やニーズの核心を突くものでした」と同社の青田 洋子氏は強調します。
導入後の成果
「今、現場に何が起こっているか」を把握し、迅速な対応が可能に
こうして同社では、IFS Applicationsをまず呉工場に適用。その1年後には、同じくIFS Applicationsをベースとするプラットフォームを長崎工場にも横展開しました。ともに、フィット&ギャップによる事前調査から、自前のシステム開発を含めたトータルな構築期間が1年間という短期導入を実現しています。
「IFS Applicationsでは、製造工程におけるプロセスフローを定義するBOP(Bill of Process)を管理できるため、同BOPを活用することで工程管理を支援するような独自システムの開発も効率的に進めることができました」とアドオンシステムのシステム開発パートナーの担当者は語ります。
導入の結果、長崎工場・呉工場で異なっていた工程の階層・メッシュを標準化。これにより、工程を一定の粒度で体系立てて管理できるようになりました。
「個別受注生産であり、しかもそれぞれ別の企業の文化を持っていた2つの工場の工程を標準化できたことは非常に大きな意義を持つと思います」と青田氏は強調します。
こうして、両工場では、当初の予定通りに生産関連情報の統合的な管理を実現。計画精度や生産性の向上という視点から、様々な成果が上がりつつあります。例えば、工程間の連動がスムーズかつ確実に行えるようになったこともその1つです。
「製造工程を進めるに当たっては、上流側で作業指導票の作成などの準備作業が必要ですが、以前はそれが後手にまわり、製造現場のほうから催促されるケースもありました。これに対し現在では、生産計画から部材や指示書の準備、そして実際の製造に至るシーケンスがシステム上で管理され、各プロセスを確実に実行していける体制が整っています。製造現場からの催促は無くなり、準備不足からの指示待ちや後戻り作業によるロスは、未然に防止されています」と池田氏は満足感を示します。
また、作業工数実績についても、これまでは月末に作業チーム単位で集計・レポート化されていました。それが今では、作業担当者各人が毎日、その日の自分の実績情報を、タブレットを使ってシステムに投入するという運用により、個々の担当者ごとの作業実績が翌日にはシステム上で把握できるようになっています。
「このように各工程についての予定と実績をより詳細かつ迅速に捉えられるようになったことは非常に大きい。例えば現場での進捗の遅れをいち早く認識し、ケースに応じて人的リソースを投入するといった迅速な対処が可能になるからです。それが現場生産能力の向上につながっています」と上河内氏は言います。
加えて、生産活動にかかわるすべてのデータが日々、IFS Applications上に蓄積され、いつでも即時に参照できることも大きなポイントです。これにより、過去プロジェクトの情報をベースとしたプロセス改善に取り組むことも容易になる上、その改善成果を適切に評価できる仕組みができました。
「IFS Applications上で生産情報が体系的に管理されるようになったことで、IoTやAI/機械学習といった先進デジタル技術の活用に向けた基盤が整備されたと評価しています」と青田氏。今後も三菱日立パワーシステムズ様では、今回構築したプラットフォームをベースに、さらなる生産管理業務の精度や生産性の向上を実現していく考えです。
お客様プロフィール
三菱日立パワーシステムズ株式会社


所在地 | 神奈川県横浜市西区みなとみらい3-3-1 三菱重工横浜ビル |
---|---|
設立 | 2014年2月 |
資本金 | 1,000億円 |
売上高 | 7,955億1,100万円(2017年3月期) |
従業員数 | 連結 18,675人 単独 10,741人(2018年4月現在) |
事業概要 | 2014年2月に三菱重工業株式会社と株式会社日立製作所が両社の火力発電システム事業を統合し誕生。「火力発電・環境技術で地球の未来を明るくする」をビジョンステートメントに、世界をリードする環境技術と高効率な火力発電技術を通じて、エネルギーと環境という地球規模の課題解決に貢献している。 |
URL | ![]() |
この事例の製品・ソリューション

本事例に関するお問い合わせはこちらから
(2019年1月29日)
関連事例
量子コンピューティング技術の活用で
複雑な生産計画立案の自動化に成功
~設備稼働率15%向上、計画立案工数90%削減を実現~
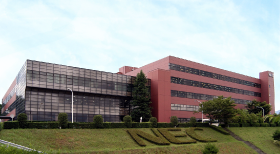
- 業種:
- 製造・プロセス
- 業務:
- 生産管理
- 製品:
- その他
戸田建設株式会社様、YKK-AP株式会社様、大和ハウス工業株式会社様
入退ゲートのその先へ 顔認証活用の新たなソリューションをめざす3社の取り組み
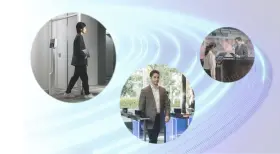
- 業種:
- 製造・プロセス
- ソリューション・サービス:
- 生体認証/その他
- 生体認証/顔認証
NECの量子コンピューティング技術でDXを加速
複雑で難解な出荷計画業務を飛躍的に効率化
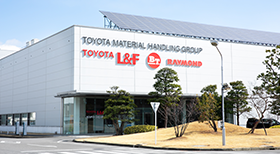
- 業種:
- 製造・プロセス
- 業務:
- 物流
- 製品:
- 統合型システム
- ソリューション・サービス:
- AI・ビッグデータ
「NEC 働き方見える化サービス Plus」の導入により、
多様な働き方の実現と生産性向上を促す仕組みの構築に貢献
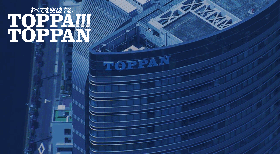
- 業種:
- 製造・プロセス
- 業務:
- 人事・総務
- 製品:
- ソフトウェア/コラボレーション
- ソフトウェア/情報管理
- その他
- ソリューション・サービス:
- 働き方改革
- クラウド
顔認証技術を活用し、多様なサービスを実現
マンションの暮らしに新たな価値を創出

- 業種:
- 製造・プロセス
- 建設・不動産
- 業務:
- その他業務
- 製品:
- その他
- ソリューション・サービス:
- 生体認証/顔認証
- サービス/その他
他の事例を探す