Japan
サイト内の現在位置
Pioneer Manufacturing (Thailand) Co.,Ltd. 様
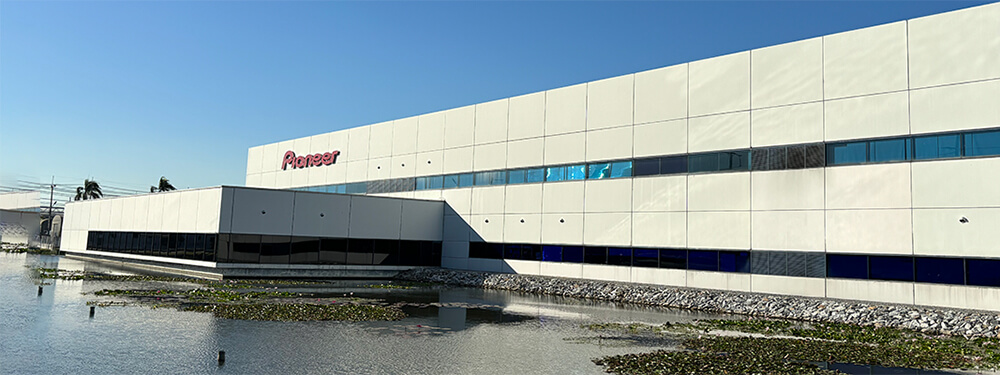
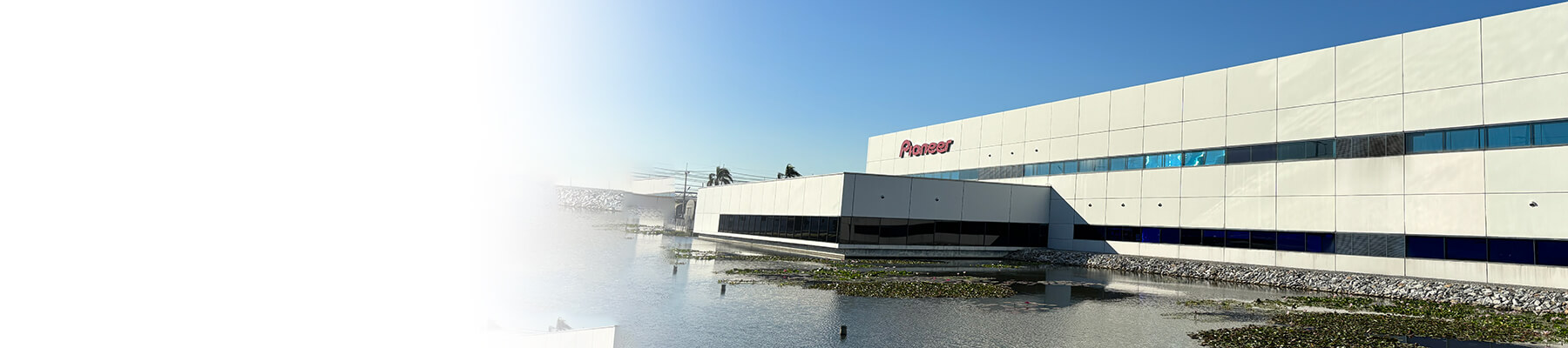
ローコード開発ツール導入でコストを抑えて周辺システムを構築
伝票処理業務のDX化により作業時間を従来の5分の1に削減
- 業種:
-
- 製造・プロセス
- 業務:
-
- 経理・財務
- 物流
- 生産管理
- 製品:
-
- 統合型システム
- ソフトウェア/開発環境
- その他
- ソリューション・サービス:
-
- 共通業務/ERP
- 共通業務/SCM
- 共通業務/その他
事例の概要
課題背景
- 基幹システムが老朽化していたが、コスト及び要員の観点から当面は既存システムの運用を継続する必要があった
- 膨大な紙の利用や手作業が随所に存在し、効率化・ペーパーレス化が必要であった
- 環境変化に即応できるよう、将来的にはシステム更新・改修を現場で行えるようにする必要があった
成果
ローコード開発ツールにより現場での自在な開発へ
現場の業務改善に必要な周辺システムをローコード開発ツールで構築することで、基幹システム自体には手を入れずに運用改善を実現。段階的なスキルトランスファーにより、各現場のスタッフが事業環境の変化に応じて迅速かつ柔軟に改修や開発が行えるようになった
自動化により、人材がより付加価値の高い業務へ
従来、人の目で照合していた資材受入や請求書チェック業務を、システム化により省力化。月500時間かけていた伝票処理業務を100時間にまで削減することに成功し、人材をより付加価値の高い業務にシフトできるようになった
ペーパーレスや在庫最適化によるムダの排除で環境に貢献
周辺システムの開発で、毎月5,000枚にも及ぶ請求書PDFのプリントアウトを一掃しペーパーレス化を実現。適正在庫の維持も可能とし、ロスの削減にも繋がった
導入ソリューション
基幹システムを改修せず、ローコード開発ツール「TALON」で周辺システムを開発
RPAやAI-OCRも活用し、人手による作業の自動化やペーパーレスを実現
基幹システムに入力されている発注データと納品物に貼られたQRコードを照合し、受入れ作業の効率化と基幹システムとの連携を実現、また、請求書(インボイス)の情報をAI-OCRでデータ化し基幹システムの発注データと照合するシステムを新たに開発。多額なコストをかけて基幹システムを改修せず、低コストのローコード開発で業務効率化が実現できた。
事例の詳細
導入前の背景や課題
老朽化したシステムには触れずに業務効率化をいかに実現させるか
カーエレクトロニクス関連製品の分野で斬新かつユニークな発想と最先端のテクノロジーを活かし、数多くの世界初・業界初の製品やサービスをグローバルに提供しているパイオニア株式会社様。最近では、ハードウェアだけでなく、安心・安全なモビリティ社会の実現に向けて、膨大なモビリティデータやカメラの映像データ、位置情報を活用し、クラウドと連携したソリューションも提供しています。
そんなパイオニアグループにあって、カーナビゲーションシステムやカーオーディオ製品の生産を担い、グループ最大の生産量を誇る製造拠点がPioneer Manufacturing (Thailand) Co.,Ltd.様(以下、タイ工場)。2024年に設立30周年を迎えます。
同社では、設立当時に導入した基幹システムを、今日までシステム改修を重ねながら使い続けてきましたが、日本本社のシステム共々老朽化が進み、刷新する計画が進んでいました。しかしながら、本社システムの刷新が想定以上のコストを要することとなり、タイ工場分は見送られることとなったのです。
したがって、システム刷新を前提に様々な業務効率化を進める計画は一旦ストップ。旧来の基幹システムを使い続ける前提で考え直す必要に迫られました。
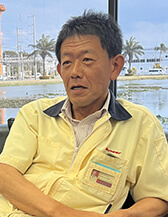
Production Control & Procurement Management Division
Senior General Manager
和田 嘉弘氏
システム化による省力化が待ったなしの業務には、次のものがありました。まず、パーツなど納入資材の受入業務。それまで、資材が納入されると、基幹システムの発注情報と一つひとつ担当者が目で照合し、合っていれば基幹システムに入力し在庫情報としていたのです。「この作業に多大な手間と倉庫内のスペースを要していました」とタイ工場で生産や物流の管理を担っている和田嘉弘氏は言います。
経理面では、請求書のチェック業務。毎月5,000枚ほどの請求書がPDFで届くと、いちいちプリントアウトして、同様に担当者が一枚一枚目で基幹システムの発注情報と照合していました。
「当該業務全体で、毎月500時間ほどかかっていました。また、人の目による照合ミスも発生していました」と経理部門の遠藤英太朗氏は打ち明けます。
これらの業務効率化は、すぐにでも手を打つべき状況にありました。
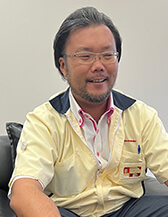
Administration & Accounting division
General Manager
遠藤 英太朗氏
選択のポイント
多額なコストをかけず開発できる周辺システムで課題を解決
「そこで、以前から取引があり、システム面で何かと相談させてもらっていたNECタイさんに、今回もQRコードを用いた受入システムなどがつくれないか相談を持ち掛けたのです」と和田氏は言います。
タイ工場のシステム事情を把握していたNECタイの松原氏は、改修に多額のコストを要する基幹システムはリプレイスできないこと、先方には自らシステム開発も行えるITシステム部門があるものの多忙を極めていること、激しい環境変化があっても柔軟にシステム改修が行えること、といった観点から、「TALON」による周辺システム開発を提案しました。
NECが取り扱う「TALON」は、基本的にブラウザ上で様々な設定を行うことでシステムを組むことが可能で、一部プログラミングが必要となるローコード開発ツール。UIとしては、単票や明細、カレンダー、グラフ、ガントチャートの各表示機能が用意され、つくった機能をユーザーごとに好みのUIに改造することもできます。
「当初は我々がシステム開発までお手伝いしますが、現場の方に徐々にスキルトランスファーを行い、ゆくゆくは現場の方々だけで開発できるようにすることがご提案のポイントでした」
NECタイが提案した受入システムは、納入された資材に貼られているQRコードをスキャンすると、基幹システムの発注情報と自動的に照合を行い、在庫情報を更新するとともに、在庫移動先のロケーション指図を行う。
請求書照合システムは、届いた請求書をAI-OCRが読み込んでデータに変換し、基幹システムの発注情報と自動的に照合し、会計システムへ支払い情報の連携を行う。
「いずれも、基幹システムには一切触れず、最大の懸案であった多額のコストをかけずに大幅な業務効率化が実現できる上、『TALON』ならいろいろなものができそうなところが非常に良かったと思います」と、和田氏はNECタイの提案を受け入れた要因を話します。
導入後の成果
ムダを削減し、人材をより付加価値の高い業務にシフト
2020年の12月頃に和田氏からの相談を受け、NECタイは2021年1月に提案を行い、3月に正式に受入システムの開発がスタート。同年8月から稼働を始めました。
請求書照合システムは、受入システムの好評価を確認後、同年10月から開発に着手し2022年12月から稼働を開始しました。その成果について、和田・遠藤の両氏は次のように評価しています。
「受入システムによって、担当者を半減させることができました。減らせた分は、人にしかできない高付加価値の業務にシフトできています。また受入前後での在庫の滞留が減ったことで、倉庫内のスペースが確保できたことにより、従来外部に委託していた倉庫費用もゼロにすることができました。」(和田氏)
「まずは主要なサプライヤーの請求書から始めたのですが、この請求書の照合業務だけで1ヶ月間で約500時間の工数を掛けていたものが200時間まで減りました。そこで、スキルトランスファーを受けて弊社だけでもシステム開発ができるようになっていたことから、対象とするサプライヤーを広げ、今では98%の請求書をこの照合システムに対応させています。この業務に掛ける工数は100時間を切るまで減らすことができました」(遠藤氏)
これらの成果を受け、第3弾となる「かんばんシステム」も開発しています。部品などが所定の在庫数まで減ったところでサプライヤーに発注をかけることで、余計な在庫を抱えないための仕組み。従来は、これも手作業で残量を割り出し発注をかけていましたが、人力では限界があり一部のサプライヤーに止まっていたのです。これをシステム化することで、対応サプライヤーを大幅に広げる見込みです。
サステナビリティ推進への貢献
気候変動などの問題が顕在化し、持続的成長を支える経営基盤としてESG(環境・社会・ガバナンス)対応が不可欠との認識が広がっています。
こうした中にあって、パイオニア様はグループを挙げてサステナビリティに熱心に取り組んでいます。今回のシステム化により、毎月5,000枚ものプリントアウトが不要となりペーパーレス化に繋がったほか、適正在庫の促進によるロス撲滅に繋がっています。加えて、人材が単純作業から解放され、より創造的な業務にシフトでき働きがいが向上した効用も。
「当社グループのサステナビリティ推進に貢献できていると自負しています」と遠藤氏は言います。
今後のビジョンやNECへの要望について、和田氏は次のように話しました。
「NECさんからは、生産計画の並び替えなどをAI化することで状況変化に瞬時に対応できるようになると聞いています。こうした技術的な進化について情報をもらえることは大変助かっています。我々も常に進化させていきたいので、今後も継続的な情報提供や提案を期待しています」
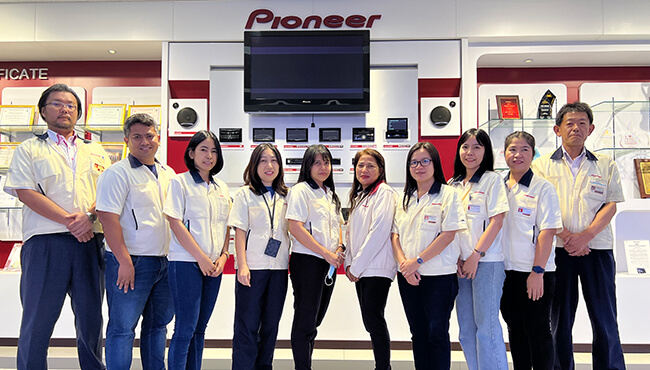
NEC担当スタッフの声
お客様の環境変化に迅速に対応しシステム改修できるソリューションをご提案
パイオニアのタイ拠点様においては、これまで基幹システムを自社のIT部門で、あるいはSIerの協力を得ながら改修を重ね、使い続けて来られました。ここ数年、自社IT部門への要求が非常に多く、慢性的に多忙な状況が続いていました。これによって迅速な改修が難しく、業務効率化がなかなか進まない状況にあることを理解していました。
そんな中で和田様から受入システムのご相談を受けたわけですが、すぐに当時広まり始めていたローコード開発ツールの活用を思いついたのです。従来のシステム開発のようなフルのプログラミングを必要とせず本格的なシステムを構築できるからです。
とは言え、システム設計やプログラミングが必要な部分が残るので、まずは我々が開発面では全面的にご支援し、その後スキルトランスファーを段階的に行いながら最終的にはお客様のほうで全面的に自在に改修や開発をしていただこうと考えました。
なぜならば、特にカーエレクトロニクス用品を提供しているパイオニア様は、グローバルであることや自動車産業に関わる上で一段と環境変化が激しく、システムの要件も環境変化に応じて迅速、柔軟に変えていくことが求められるからです。
今回は、多額なコストや手間を要する基幹システムには触れないことも併せて、お客様からご評価いただけました。NECが製造業として自社の生産現場で実践した内容をご提案できている点も、ご信頼いただけているポイントであると自負しています。
今後も、お客様の業務課題や環境変化への対応に貢献すべく、有益なソリューションを提供し続けることを弊社の価値と捉え、日々活動していきたいと思います。
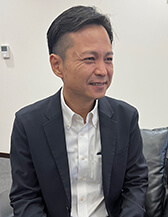
Manufacturing & Automobile Solution Division
Senior Manager
松原 繁氏
お客様プロフィール
Pioneer Manufacturing (Thailand) Co. ,Ltd. 様
所在地 | Rojana Industrial Park, 1/31 Moo 5 Tambol Kanham Ambphur U-Thai, Pranakornsriayutthaya 13210, Thailand |
---|---|
創業 | 1994年 |
資本金 | 23億円 (600M THB) |
売上高 | 830億円(2023年3月期)(21,230M THB) |
従業員数 | 1,127名(2023年12月31日現在) |
事業内容 | カーエレクトロニクス関連商品の製造 |
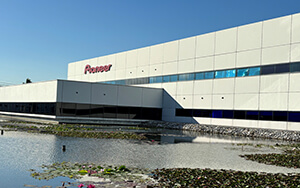
(2024年2月6日)
同じ製品・ソリューションの導入事例
量子コンピューティング技術の活用で
複雑な生産計画立案の自動化に成功
~設備稼働率15%向上、計画立案工数90%削減を実現~
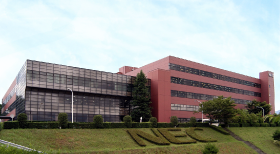
- 業種:
- 製造・プロセス
- 業務:
- 生産管理
- 製品:
- その他
戸田建設株式会社様、YKK-AP株式会社様、大和ハウス工業株式会社様
入退ゲートのその先へ 顔認証活用の新たなソリューションをめざす3社の取り組み
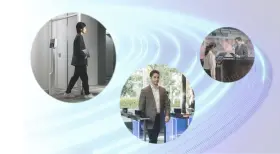
- 業種:
- 製造・プロセス
- ソリューション・サービス:
- 生体認証/その他
- 生体認証/顔認証
NECの量子コンピューティング技術でDXを加速
複雑で難解な出荷計画業務を飛躍的に効率化
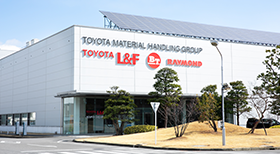
- 業種:
- 製造・プロセス
- 業務:
- 物流
- 製品:
- 統合型システム
- ソリューション・サービス:
- AI・ビッグデータ
「NEC 働き方見える化サービス Plus」の導入により、
多様な働き方の実現と生産性向上を促す仕組みの構築に貢献
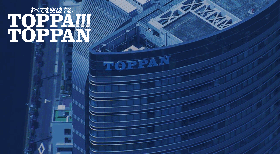
- 業種:
- 製造・プロセス
- 業務:
- 人事・総務
- 製品:
- ソフトウェア/コラボレーション
- ソフトウェア/情報管理
- その他
- ソリューション・サービス:
- 働き方改革
- クラウド
顔認証技術を活用し、多様なサービスを実現
マンションの暮らしに新たな価値を創出

- 業種:
- 製造・プロセス
- 建設・不動産
- 業務:
- その他業務
- 製品:
- その他
- ソリューション・サービス:
- 生体認証/顔認証
- サービス/その他
他の事例を探す