Japan
サイト内の現在位置
バイオプラスチック
NECの最先端技術2016年8月

NECでは環境対策への取り組みとして様々な活動を行っており、研究開発の面でも環境負荷を削減するための技術開発を進めています。その一つに、最近話題となっている、環境調和性に優れた植物を原料とした バイオプラスチックの研究があります。
2006年には、バイオプラスチックを外装全体に採用した携帯電話(FOMA-N701iECO)を製品化(2006年3月2日プレスリリース)、2010年1月には、パソコン筐体に使われる プラスチックの約90%に、世界最高水準の環境調和性を実現した難燃性バイオプラスチックを採用したビジネスパソコンを製品化しています。
その際、NECが開発するバイオプラスチックを「NeCycle™」と名付けました。

ここでは、私たちが開発してきた電子機器用の環境調和型プラスチックとして、はじめに取り組んだ安全性に優れた石油系の難燃性プラスチックについて述べ、さらに一層の環境調和性の向上のため、近年、開発に注力してきたバイオプラスチック(NeCycle™)について詳しく紹介します。
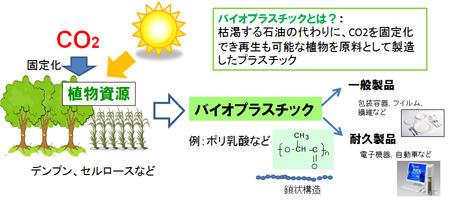
1.石油系の環境調和型難燃性プラスチックの開発
私たちは環境調和性に優れたプラスチックの開発を約10年前に始めました。当時、電子機器分野でこの概念の材料はほとんどなく、パイオニアの一人としての出発でした。はじめに着手したのが、従来の石油を原料とした難燃性プラスチックの環境安全対策です。電子機器に使用するプラスチックは、火災防止のために燃えにくいこと、つまり難燃性が必要ですが、従来のプラスチックは、ハロゲン系化合物などの難燃剤を添加することで難燃化を実現していました。しかし、このようなハロゲン系難燃剤は燃焼時に環境負荷の高い物質を発生し、また、この代替材として使用が開始されていたリン化合物にも慢性毒性が懸念されるなど、環境安全性が十分でないものが主体でした。
そこで私たちは、脱ハロゲン脱リンによる高度な難燃性を実現し、環境安全性を大幅に向上できる難燃性プラスチックの開発に取り組み、電子機器用として初めて実用化に成功しました( 参考文献1 )。すなわち、着火時に樹脂表面に難燃層を形成できる独自なシリコーン系難燃剤を使った難燃性ポリカーボネート樹脂(エコポリカ™)を開発しました。エコポリカは、材料メーカーとの共同で製品化され、現在、NECのパソコンやプロジェクタなどの環境対応機器の中心的な外装材として利用され、さらに他の分野の様々な用途でも利用されています。また、着火した際に樹脂自体が発泡化して断熱層を形成することで、難燃剤無添加でも自ら消火が可能なエポキシ樹脂(自己消火性エポキシ樹脂)も開発しました。この自己消火性エポキシ樹脂は、ICパッケージ用モールド材として、材料メーカーと共同で製品化され、NECに加え、世界の主要なデバイスメーカーで広く採用されています。
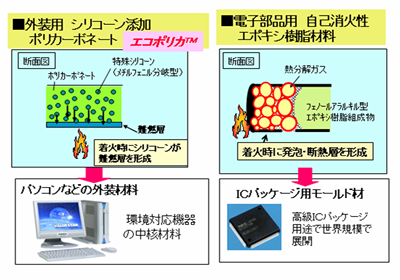
参考文献1) 位地 正年, 化学工業, 6,46-53 (2000).
2.石油系プラスチックから植物性プラスチックへ
先に述べたように、従来の電子機器の外装や電子部品の絶縁材料には石油を原料としたプラスチック(ポリカーボネート、ABS、エポキシ樹脂など)が用いられており、環境安全対策は進みつつあります。しかし、現在、石油資源の枯渇が顕在化しつつあり、再生可能な資源への代替化が新たな課題となってきています。
これに対して、植物を原料としたバイオプラスチックは、植物原料が石油原料の代わりになる上、植物に地球温暖化の要因とされている二酸化炭素を固定化する効果があり、さらに、廃棄後、土の中での分解性(生分解性)に優れているという特徴もあるので、 新たな環境調和材料として、現在、大きな期待が寄せられています。
3.バイオプラスチックの取り組み
バイオプラスチックは、微生物生産系、化学合成系、天然物系の3つに分けられます。中でも化学合成系のポリ乳酸は、トウモロコシを原料として量産化が開始され、さらにバイオプラスチックの中では比較的に耐熱性が高いため、電子機器外装材の一部に採用が始まっています。
しかしながら、電子機器に広く使用するためには、ポリ乳酸の一層の高機能化が必要です。すなわち、従来の石油系プラスチックに比べ、特に耐熱性と強度(衝撃強度など)が劣っており、さらに、安全な難燃化処方(脱ハロゲン化)が確立されておらず、加えて、成形した際の結晶化速度が遅いため生産性の向上も必要です。これらを解決するための技術開発は各社で進められていますが、従来は、石油系プラスチックなどの石油成分を大量に(約50%)添加する処方が主体であり、ポリ乳酸のバイオプラスチックとしての高度な環境調和性を低下させてしまう問題がありました。
これに対して私たちは、ポリ乳酸の環境調和性(高植物成分率+安全性)を保持しながら高機能化して電子機器に適用することを目指して、植物資源を主体として実用特性を改良し、さらに、従来にない新機能を付与することで、付加価値を高める研究を進めています( 参考文献2、3 )。すなわち、ポリ乳酸への温暖化防止効果の高いケナフの繊維などの植物系添加剤の利用による高耐熱化と高強度化、ハロゲン等の有害物を一切使わないで安全な吸熱剤(金属水酸化物)の添加による難燃化、さらに、これまでにない新しい機能として、形状記憶性とリサイクル性の同時実現などに取り組んでいます。
参考文献2) 位地 正年, 未来材料, 6,22-26 (2006).
参考文献3) 位地 正年, 工業材料, 56,2,45-49 (2008).
ケナフ繊維添加ポリ乳酸
ポリ乳酸を電子機器の外装材料に使用できるようにするためには、耐熱性、強度、さらに成形性のレベルを大幅に向上させることが必要です。そこで、ケナフ繊維などの植物系添加剤を利用して改良したケナフ添加ポリ乳酸複合材を開発しました。本材料は、電子機器用バイオプラスチックとしては、最高レベルの植物成分率(無機物を除く樹脂分中)90%を実現しました。
ケナフとは、アフリカ原産の植物で、二酸化炭素の吸収速度が植物の中でも最高レベル(光合成速度は、通常の樹木の3~9倍、1トンのケナフで約1.4トンの CO2を吸収することが可能)であり、地球温暖化防止効果の高い植物といわれています。現在、東南アジアをはじめ世界各国で栽培されていますが、その利用方法としては、紙の繊維材料や飼料など既存の材料の代替が主であり、付加価値の高い利用方法はほとんど見いだされていませんでした。
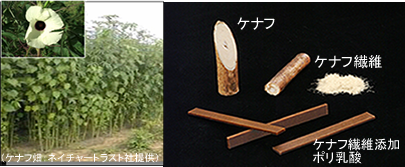
そこで、ポリ乳酸にケナフ繊維を添加、混練りして補強効果を調査した結果、ケナフ繊維を15%以上添加すると、石油系プラスチックのABS樹脂以上に耐熱性(荷重たわみ温度)と剛性を大幅に向上させることを発見しました。これは、ケナフ繊維が、樹脂の変形を防止しただけでなく、ポリ乳酸の結晶化を促進する効果もあったことが起因しています。さらに、ケナフの微粉を取り除いたり、植物原料系の柔軟性付与材を添加することで衝撃強度も改善できました。また、ケナフ繊維と新しい結晶化促進剤の併用により、成形時間の大幅な短縮化にも成功しました(従来10分間以上が1分間以下)。
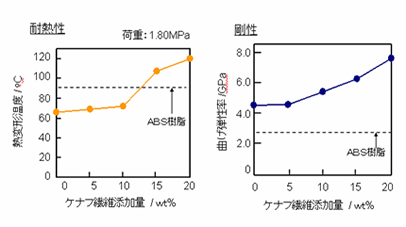
このケナフ添加ポリ乳酸複合材は、材料メーカーとの共同で製品化され、2004年9月にパソコンのダミーカードに搭載され、さらに、2006年3月にエコ携帯電話に搭載されました(写真)。この携帯電話は、世界で初めてバイオプラスチックを筐体に全面的に使用し、さらにこの素材感を生かしたデザインを採用したこと(やわらかな癒しを感じさせる調色と、素材の感触を生かすため厚い塗装なし)が特徴であり、大きな反響を得ました。
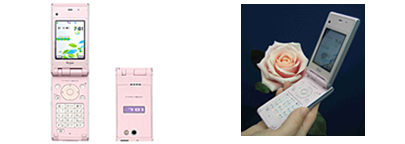
難燃性ポリ乳酸複合材
パソコンなどの中型以上の電子機器用の外装材料としては、プラスチックには高度な難燃性も要求されます。しかし、ポリ乳酸は燃焼しやすいので、難燃性を向上させる必要があります。上述のように従来のハロゲン系難燃剤は環境安全性が十分ではないので、これらの添加物を使用しないでポリ乳酸の難燃化を実現させることを目指しました。
ポリ乳酸への難燃剤として、安全性の高いさまざまな材料を検討した結果、特に土壌成分の一種である特殊な金属水酸化物の吸熱剤と他の安全な添加剤を併用して使用することで、高度な難燃性と他の主要な実用性(強度、耐熱性など)を同時に実現させることに成功しました。
そしてこの材料技術に改良を重ね、2009年11月には、植物由来成分75%以上配合(有機成分中)、製造・成形時のCO2発生量も従来の石油系難燃性樹脂(PC/ABS)に比べ50%削減するなど、世界最高レベルの環境調和性と、難燃性等の実用性を実現した難燃性バイオプラスチック(難燃性ポリ乳酸複合材)を初めて実用化しました。
この材料は、環境対応を強化したビジネス向けパソコンに採用され、製品に搭載されています。
その後、業務用端末、プロジェクター、POS (店舗販売管理システム)の部材にも適用が拡大されました。さらに、他の電子機器や様々な耐久製品にも利用を拡大するため、新たに、耐薬品性、耐光性、傷防止性などの高い耐久性や抗菌性も実現しました。これらの特性は、従来の電子機器用の石油系難燃性樹脂(例PC/ABS樹脂)より優れており、これまでの高度な環境対応に加え、難燃性樹脂としての付加価値を向上できました。このため、本材料をNECがこれから注力していく社会ソリューションに関連する設備や装置(交通、流通、金融関係など)に利用を拡大していく予定です。この手初めとして、厳しい外部環境にさらされる屋外設備であり、高度なガソリン耐性や寸法安定性なども要求されるガソリン給油システムの内部部材として利用を開始しました。→ 2014年6月30日プレスリリース




形状記憶性バイオプラスチック(リサイクル可能な形状記憶性ポリ乳酸)
ポリ乳酸はまだ高価であるため、環境調和性に優れているだけでは、広く普及させることには限界があります。これに対しては、従来にない機能を付加することで高い付加価値を創出させることが一つの解決方法です。そこで、私たちは、従来の石油系プラスチックでも達成できていない新しい機能として、形状記憶性とリサイクル性を同時に実現するポリ乳酸を開発しました。
形状記憶性プラスチックとは、熱と外力で変形させることができ、冷却して固化しても再び加熱すると、元の形に復元できるプラスチックです。一般的に、高分子が架橋構造(網目状構造)を持つ場合、このような特性を発現できます。しかし、この架橋構造のため、高温でも溶融できず、リサイクル(他の形に再成形)は困難でした。
これに対して、ポリ乳酸に熱可逆結合を付与して架橋させることによって、形状記憶とリサイクルを始めて同時に実現できました。すなわち、この架橋構造によってヘヤドライヤー程度の加熱(60℃くらい)で形状の変形と復元が可能であり、しかも、通常の成形温度の高温(160℃)で加熱すると、架橋構造中の熱可逆結合が解離するため溶融できるので、リサイクルもできるようになりました(図:熱可逆結合による形状記憶性とリサイクル性の両立)。
このリサイクル可能な形状記憶バイオプラスチックは、ユーザーが自由な形に変形させて使用できる新しい製品、例えば、将来のウエアラブル電子機器などへの利用が考えられています。(図:ユーザーが形状を変えられる自由形状機器の例)
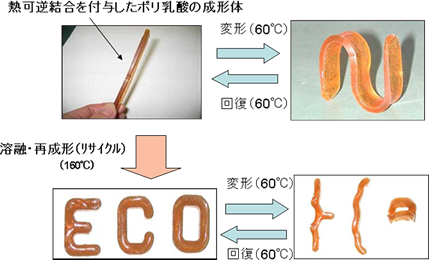
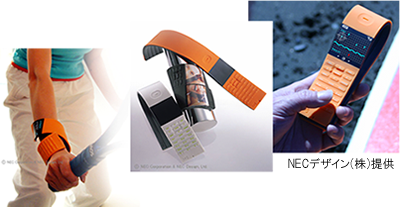
高熱伝導性ポリ乳酸複合材
先に述べた形状記憶性に続き、ポリ乳酸の付加価値を一層向上させるため、最近の電子機器で特に重要な課題になっている放熱対策に貢献できる高熱伝導性のポリ乳酸複合材を開発しました。すなわち、小型化や薄型化が進められる最新の電子機器では、内部のデバイスの発熱による筐体の高温化が問題になっていますが、これらの電子機器では、機器内部の設置スペースが限られるため、従来のファンやシート等の放熱部品の適用は難しくなっています。また、ステンレスなどの金属を筐体材料に利用した場合には、厚み方向の伝熱性が高いため、デバイス周辺部に局所的な高温部が生じ、使用時の不快感を招きやすくなります。しかも、金属はプラスチックに比べて比重が大きいため、軽量化しにくく、複雑な形状の成形に手間がかかるという課題もありました。
そこで従来から、プラスチックを高熱伝導化する方法として、石油系プラスチックに熱伝導性の高い金属や炭素等の粉体や繊維を高配合(50%以上)することが行われていますが、成形性、強度等の低下や比重の増加という実用上の課題がありました。さらに、プラスチック自体が石油原料であるために、環境対策も不十分でした。
これ対して我々は、バイオプラスチックのポリ乳酸をベース樹脂として、独自な植物原料の結合剤を用いて炭素繊維を樹脂中で網目状に結合(架橋化)させ(図8)、従来に比べて大幅に少ない炭素繊維の添加量(10%~)でポリ乳酸を高熱伝導化させることに成功しました。本材料は、ポリ乳酸とほぼ同等の低い比重(~1.3)であり、プラスチック本来の軽量性を保持しながら、ステンレス以上の熱拡散性を実現しました(図9)。さらに、成形時の炭素繊維の配向によって、金属にはない平面方向への異方的な伝熱性も達成しました(図10)。これらの特性によって、本材料を今後主流の薄型・小型電子機器の筐体材料などに利用した場合には、局部的な高温化を防ぎながら筐体全体で放熱することが可能です。さらに他の様々な分野での利用も考えられます。
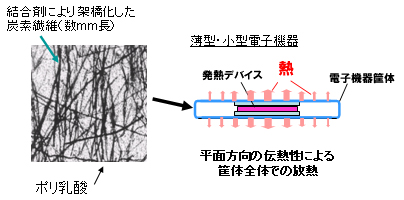

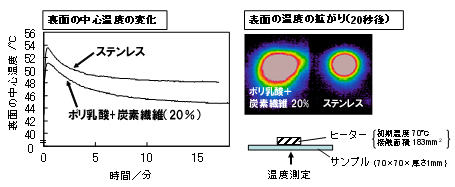
バイオプラスチックを強靱化する3層構造ナノフィラー
バイオプラスチックのポリ乳酸樹脂には、今後の薄型・小型機器に対応するため、さらなる強靱性の向上が求められています。そこで我々はこの課題を解決する技術として、3層構造のナノサイズの粒子状充填材(ナノフィラー)を開発し、この添加によってポリ乳酸の大幅な強靱性アップに成功しました。
この技術は、先に紹介した我々の高機能バイオプラスチック(ケナフ繊維添加ポリ乳酸、難燃性ポリ乳酸、形状記憶性ポリ乳酸、熱伝導性ポリ乳酸)のいずれにも適用可能な共通基盤技術になりえます。
今回開発の3層構造のナノフィラーの特徴は、3ユニットからなる特殊な有機ケイ素化合物の凝集と分子間の反応による架橋化*によって、自己組織的に、3層の異なる機能をもつナノサイズの粒子を形成できることです。従来、多層構造のフィラーを形成するには、何段階もの表面処理や処理剤の分離回収の工程が必要で手間がかかり、特にナノサイズの場合、実質上、製造は困難でしたが、今回、初めて効率的よく3層構造を形成させることが可能となりました。
このナノフィラーの構造は、中心に高密度(高剛性)のシロキサン、中間層は可とう性(柔軟性)のあるシリコーンゴム層、そして外側はポリ乳酸との親和性の高い有機層(カプロラクタムオリゴマー)となっています。このため、ポリ乳酸に混ぜた時、通常の無機フィラーのような剛性とともに、ゴム層による応力吸収性や、有機親和層による樹脂の伸びを改善する効果があります。この結果、このナノフィラーをポリ乳酸へ少量(重量の5%)添加するだけで、ポリ乳酸の強度を保持しながら破断伸びを2倍以上向上させることができます。

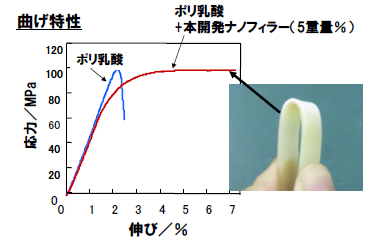
本技術は、外装用のバイオプラスチックの強靱化に有効であり、バイオプラスチックを使った電子機器筐体の薄型化や耐久性の向上などに寄与するものと考えます。さらにこのナノフィラーの構造の最適化やコストダウンを進め、実用化を目指します。
- *架橋化:鎖状や枝状をポリマー同士が結合(橋かけ)し、網状の構造にすること。
非食用の植物資源を用いて高植物成分率と耐久性を両立したバイオプラスチック (植物の茎とカシューナッツの殻の成分を利用したカルダノール付加セルロース樹脂)
このたび、安定した供給性のある非食用の植物原料として、植物の茎などの主成分のセルロースとカシューナッツ殻の主成分のカルダノールを使って、70%以上の高い植物成分率と電子機器に必要な耐久性を同時に実現したバイオプラスチックを開発しました。
これまでご紹介してきたバイオプラスチックでは、ベース樹脂(添加剤を加える前の樹脂自体)として、量産化が進んでいるポリ乳酸を使っており、この原料としては、古くなった穀物(家畜用飼料)から採取したデンプンを主に利用しています。従って、現在、直ちに食糧問題を引き起こすものではありませんが、一方で、将来の食糧不足への懸念から、今後は、食用ではない植物資源を利用した新しいバイオプラスチックも重要となっております。
そのため、非食用の植物資源を用いたバイオプラスチックとして、セルロースやヒマシ油などを原料に用いた開発や実用化が進められています。セルロースは、草や作物の茎や木材の主成分であり、石油生産量にも匹敵する、世界でもっとも安定供給性のある非食用の植物資源です。これまでセルロースを用いたバイオプラスチックは、文具、玩具、生活用品などで実用化されています。しかし、セルロースを利用する場合、石油系の添加剤(可塑剤など)を大量に使用する必要があるため、植物成分率の低下や、耐水性、耐熱性などの高い耐久性の実現が困難という課題があります。一方、ヒマシ油を利用したポリアミドも実用化されていますが、原料の安定供給性に懸念があり、また、耐久製品に広く利用するためには特性が十分ではないなどの課題があります。
そのため、非食用の植物資源を用いたバイオプラスチックとして、セルロースやヒマシ油などを原料に用いた開発や実用化が進められています。セルロースは、草や作物の茎や木材の主成分であり、石油生産量にも匹敵する、世界でもっとも安定供給性のある非食用の植物資源です。これまでセルロースを用いたバイオプラスチックは、文具、玩具、生活用品などで実用化されています。しかし、セルロースを利用する場合、石油系の添加剤(可塑剤など)を大量に使用する必要があるため、植物成分率の低下や、耐水性、耐熱性などの高い耐久性の実現が困難という課題があります。一方、ヒマシ油を利用したポリアミドも実用化されていますが、原料の安定供給性に懸念があり、また、耐久製品に広く利用するためには特性が十分ではないなどの課題があります。
そこで我々は、これらの課題を解決するため、セルロースを主原料にして、これにカシューナッツの殻由来のカルダノールを化学結合させることで、新しいバイオプラスチック(カルダノール付加セルロース樹脂)を開発しました。カシューナッツの生産時には、食べられない殻が大量に発生しますが、ほとんど有効に利用されておらず、安定な供給性のある非食用の植物資源として期待されています。この殻の主成分として含まれる油状物質がカルダノールであり、柔軟で疎水的な直鎖状の炭化水素成分と剛直な環状炭化水素(フェノール)成分からなる特有の分子構造を持っています。このため、これを化学反応しやすく変性した後、枝状にセルロース(酢酸変性品)に化学結合させることで、高度な強靭性(強度+伸び)、耐水性、耐熱性、および非結晶性による短時間成形(石油系樹脂と同等)を実現するバイオプラスチックを作成できました。さらに、本バイオプラスチックの分子構造中の隙間を埋める(パッキング)成分として、芳香環化合物も付加させることで、強度等を一層向上できました。また、主原料として植物資源のセルロースとカルダノールを使ったことで、高い植物率(>70%)も達成しました。
さらに、このバイオプラスチックの実用化を実現に向けて、2014年には従来の1/10という低エネルギー(低CO2排出量)で合成できる新しい製造技術(「2段階不均一系合成プロセス」)を開発しました。→ 2014年5月8日プレスリリース
この新しい製造方法では、従来のように原料のセルロースを有機溶媒に溶解(均一系)させず、ゲル状に有機溶媒で膨らませた状態(不均一系)にした上で、変性カルダノール(長鎖成分)と酢酸(短鎖成分)を2段階で結合して樹脂を合成します。このため、溶液からの沈殿分離などによって生成樹脂を容易に回収できます。本プロセスは、従来の均一系プロセスの方法で必要であった、生成樹脂の析出用溶媒が不要になるため、溶媒量の大幅な削減(従来の約90%減)となります。これにより、約1/10の製造エネルギー(CO2排出量)で、高機能なセルロース系バイオプラスチックの製造が可能になり、将来量産を行う際には、製造コストの大幅な削減が期待されます。
今回開発した新製造技術に基づいて、現在の製造規模(実験室レベル)を段階的に拡大しながら量産技術を完成し、2016年度内の量産開始を目指します。さらに、電子機器に留まらず、付加価値の高い他の耐久製品や今後成長する新製品への展開を目指していきます。


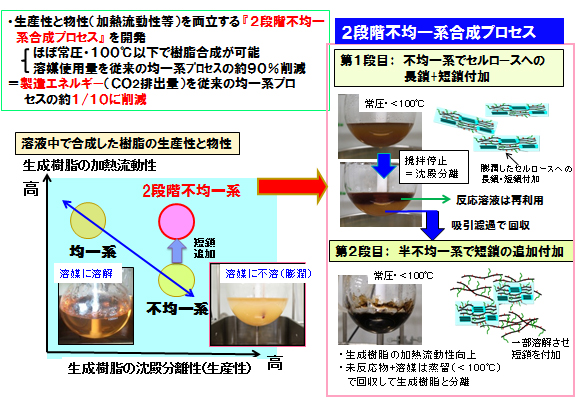
2段階不均一系プロセスの開発
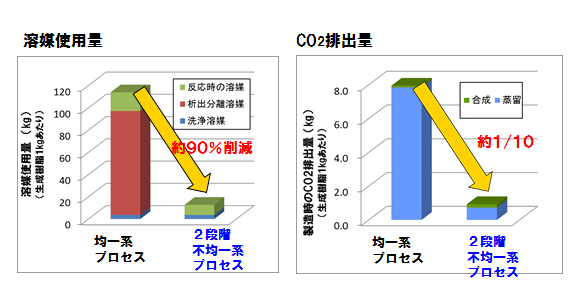
製造エネルギー(CO2排出量)の比較(実験室規模)
- ※本ページに掲載されている情報は、掲載時の情報です。
お問い合わせ