Japan
サイト内の現在位置
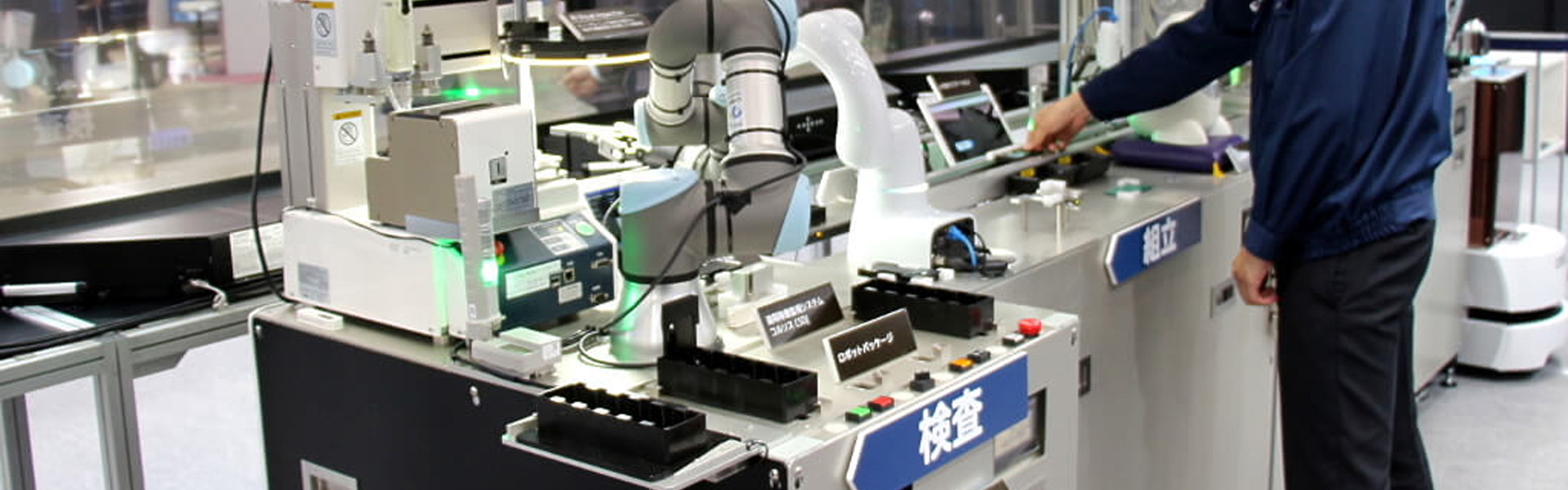
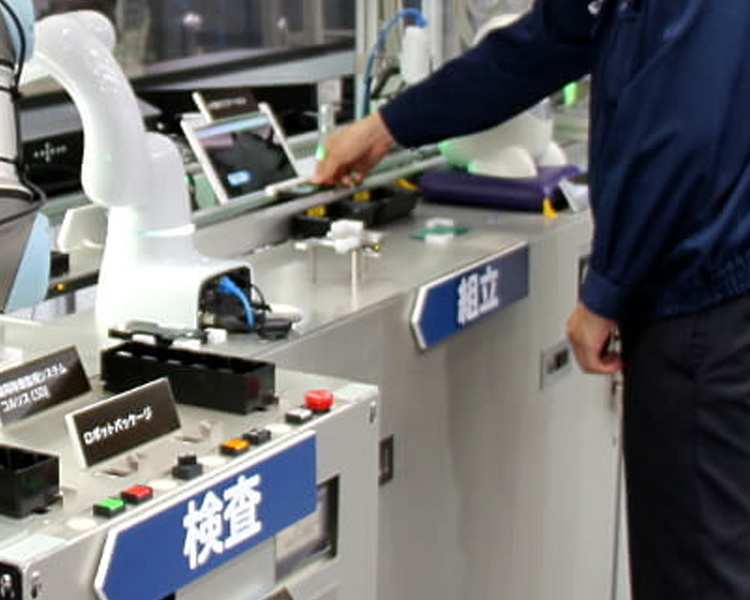
検証!ものづくり変革
――グローバルOne Factoryへの取り組み
ものづくりを支援するNECの取り組み【2019.06.25】
カテゴリ:DX・業務改革推進スマートファクトリー(IoT基盤/AI)
※この記事は、MONOistに2019年3月に掲載されたコンテンツを再構成したものです。
はじめに
IoTやAIなどの技術の発展により、製造業にもデジタル化の波が押し寄せている。ものづくりに新たな変革が求められる中で、どのような取り組みが必要になるのだろうか。新たな製造業の姿を模索するNECプラットフォームズの取締役 執行役員専務の大嶽充弘に“製造業としてのNECグループ”の取り組みを聞いた。
IoT(モノのインターネット)やAI(人工知能)関連技術の発展により、製造業の変革の動きが加速している。工場などものづくり工程のデジタル化が広がる一方、製品のIoT化によりサービスビジネスの拡大などが進みつつある。こうした大きな変化の動きの中で製造業は何を考え、どういう取り組みを進めていくべきなのだろうか。
その中で、ITベンダーとして多くの企業のデジタル変革をけん引する一方で、製造業としてものづくりに腐心する企業がある。NECだ。携帯電話端末事業からの撤退や、PC事業の合弁化など、製造業として環境変化に翻弄される中で、“製造業としてのNECグループ”はどのような変遷を遂げ、ものづくり力を高めてきたのか。
NECグループ全体のものづくり機能を集約して生まれたNECプラットフォームズの取締役 執行役員専務の大嶽充弘に、“製造業としてのNECグループ”の立場で、この変化の時代にどう取り組むのかを聞いた。聞き手はMONOist 編集長の三島一孝。
ものづくり機能を集約し再出発を切ったNECプラットフォームズ
三島:NECプラットフォームズは2017年4月に現在の体制になりました。ここまでの動きについて教えてください。
大嶽:NECプラットフォームズは2017年4月にNECグループが保有していたものづくり機能の多くの部分を集めた形で現在の姿になりました。製造拠点のものづくり機能だけではなく、開発、設計なども含めた、ICTハードウェア製品のものづくりにおけるほとんどの機能を集約したものとなります。生産拠点は国内8拠点、海外3拠点で、サーバなどのIT製品やネットワーク製品、公共システム製品や組み込み製品などを開発、生産しています。
少しさかのぼりますが、2011年にタイで洪水があった際にBCP(事業継続計画)の観点から課題が生じ、それぞれ縦割りだったハードウェア製品の製造部門を一元化し、NECグループ全体で変化、変動への柔軟性を高めようという動きが生まれました。ただ、製品の提供において「ハードウェアを作る」だけでは付加価値を生み出すことは難しく、開発設計部門も統合して、モノを通じた顧客価値の創造ができる体制となったわけです。
三島:NECでは、ものづくりの領域で、生産革新活動に積極的に取り組むなど、さまざまなノウハウを蓄積し、豊富な知見があります。
大嶽:バブル経済の崩壊後、国内に残った工場は、従来以上に生産活動のレベルを引き上げる必要がありました。そこで、NECでは1993年からトヨタ生産方式をベースに生産革新活動を推進し、無駄取りに徹底的に取り組んで、生産リードタイムの短縮と原価低減を実現してきました。
これらの工場単位でのプロセス整備や生産革新活動がNECグループ全体に広がり、2000年からは開発、調達、生産、物流、販売をカバーするサプライチェーン効率化に向けた活動に注力しました。かんばん方式をNECグループ全体に広げ、全国の物流網整備や物流ターミナルでの荷ぞろえのシステム化を実現しました。これらの過程で、グループ横断での生産革新活動なども進め、人材育成にも注力してきました。その結果、多くの生産革新人材が育ち、現在の「NEC ものづくり共創プログラム」や「NEC Industrial IoT」における「匠」人材になっています。
その後、2011年のタイの洪水により通信機器の工場が浸水被害を受け、タイ工場の製品の一部を国内に移管して生産するという対応を取りました。ただ、生産システムなどの違いで想定以上に苦戦しました。その結果、先述したようにBCPなどの観点から複数の工場があたかも1つの工場のように機能する仕組みとしての「グローバルOne Factory」というコンセプトが生まれました。
「グローバルOne Factory」に向けた取り組み
三島:「グローバルOne Factory」に向けた取り組みについて具体的にはどのような取り組みを行っているのでしょうか。
大嶽:「グローバルOne Factory」とは、もともと工場リソースの柔軟な活用を目指して生まれたコンセプトですが、現在は、ものづくり拠点間の連携を進める「協調」と、顧客と当社の緊密な連携を実現する「共創」の2つの方向性で取り組みを進めています。国内外の開発、生産拠点があたかも1つの工場のように振る舞い、常に顧客の困りごとの解決を志向した製品やサービスを提供するというコンセプトです。
ただ、「1つの工場のように」といっても実際に生産対象の製品は多岐にわたり、生産数量や時間軸、作り方や必要な設備なども異なります。人工衛星に使用される装置のような一品モノから、ルーターやサーバといった量産品に近いものまで存在します。そこでNECプラットフォームズで生産している製品の生産類型を作り、標準化を進めました。
生産方式によってI~IV類に分類し、量産品として生産しているものはI類、一品モノはIV類としました。I類の中で、一部カスタムなどが入るものについてはII類とし、IV類の中で生産に共通部分が含まれるものをIII類と位置付けています。こうした考え方で、製品を4つに類型化し、I類からIV類までの共通点や相違点を理解しながら、標準を作っていきました。標準ができれば、製品によって自在に作る工場を振り分ける、いわゆるロケーションフリーなものづくりができるようになります。そうした将来像を見据えて、仕組みのさらなるブラッシュアップを進めております。
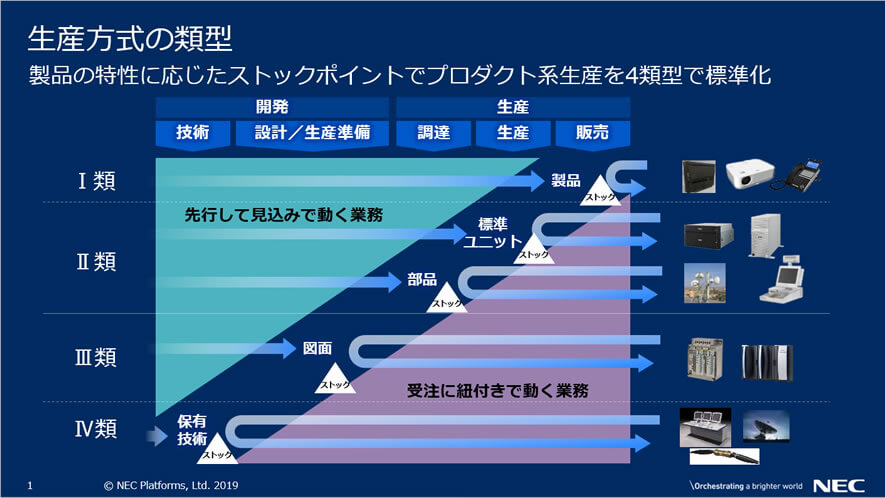
グローバルOne Factoryの実現には、工場間のシステム統一が不可欠です。2014年度からシステム統一の社内プロジェクトを推進してきましたが、2017年度に最終段階に入り、国内の基幹系ITシステムについては2018年5月に、QMS(品質マネジメントシステム)についても11月に統合を完了しました。仕組みが共有され、リモートでも現場を見る環境ができたので、それぞれが何をやっているのかが分かるようになりました。
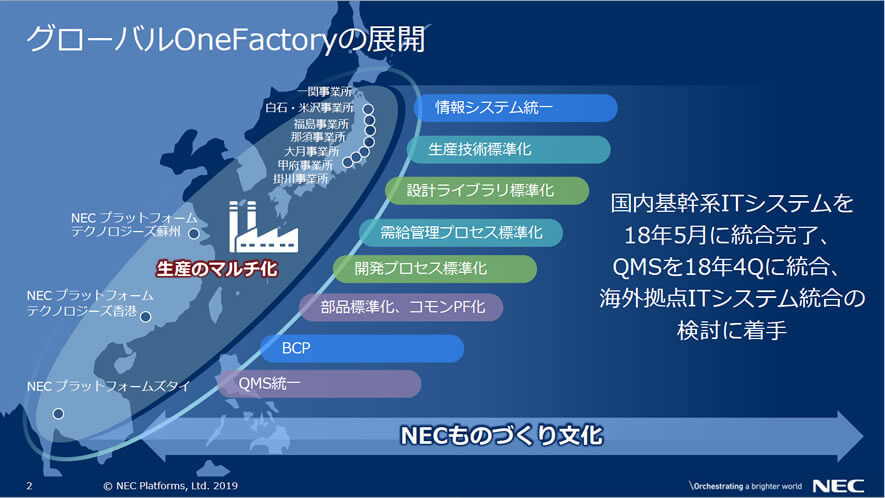
これまで、多岐にわたる類型のものづくりを個々の生産工場主体で進めてきたことから、生産工場に固有の文化が生まれ、同じ用語を使っていても定義や認識が異なっている場合がありました。このような違いを吸収し、NECグループとして統一されたものづくり文化を創らねばなりません。その為に、生産革新活動では、拠点を横断した横串ワーキンググループ(WG)を作っています。モジュール(SMT、表面実装技術)WGや物流WGなどそれぞれの工場の持つ生産革新のノウハウをテーマごとにすり合わせて、それぞれの生産性改善につなげるなど、言語や基準の共通化による効果が出始めています。
ここに掲載した「グローバルOne Factory」に向けた取り組みの他、顧客価値創造に向けた価値評価の軸やデジタル化のメリットについて話は続きます。「MARKETING DATA」のコーナーにて全文掲載したPDF資料を配布しておりますので、ご興味の方は是非ダウンロードください(無料)。
関連リンク
製造業のデジタルトランスフォーメーション
製造業にもデジタル化の波が押し寄せ、新たなビジネスモデルへの変革が進んでいます。NECが誇る先端技術と、自らが取り組んできたものづくり革新やIoT実証・実装の知見をベースに製造業のデジタルトランスフォーメーションを牽引するのが「NEC Industrial IoT」です。
お問い合わせ