Japan
サイト内の現在位置
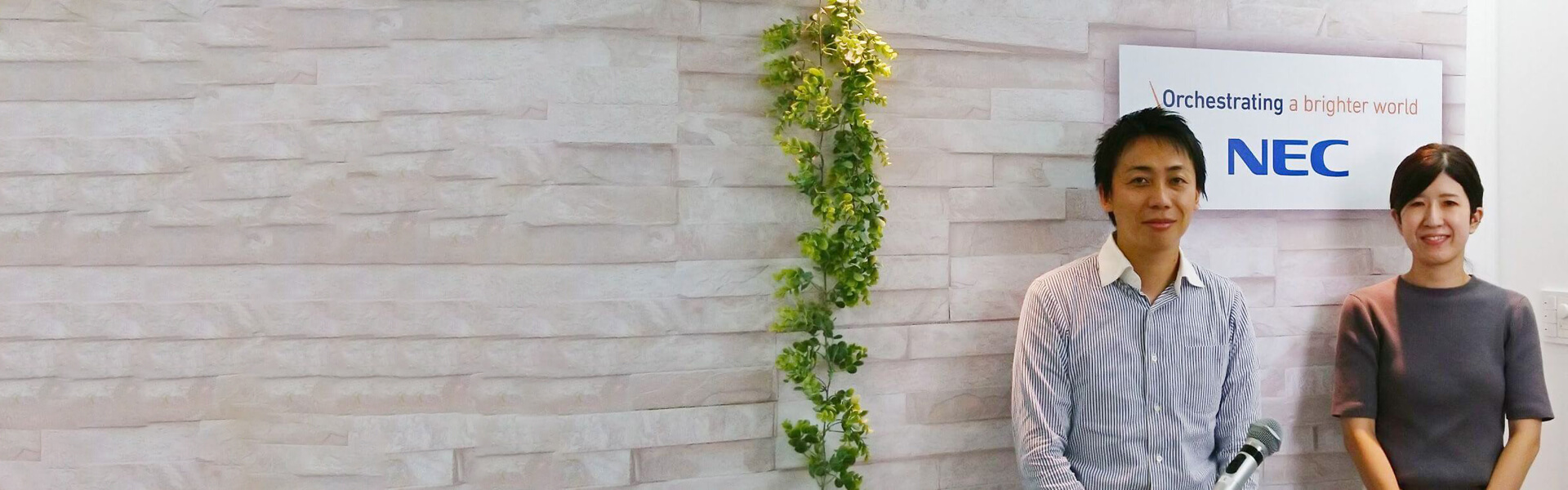

NECの考える デジタルエンジニアリング活用とは
ものづくりの未来
Webセミナーレポート 【2020.09.18】
カテゴリ:設計・開発・技術PLM/CAD
製造業は今、世界の不確実性の高まりの中で、企業変革力(ダイナミック・ケイパビリティ)の強化が求められています。 企業変革力の強化のためには、ものづくり工程全体におけるデジタル技術の活用と、 ものづくりの上流にあたる設計力の強化戦略が重要となります。
9月18日に行われたWebセミナーでは、製造業の抱える課題・重要戦略に対し、製品および工程設計力をデジタル技術によってどのように強化し、 またデジタル技術を全社で活用できる仕組みを構築していくかを、お客様事例・ユースケースを交えながらご紹介しました。
講師:NEC 井手さくら
NEC 今西一夫
“デジタル化”で設計力を強化するポイント
人手不足、不安定な国際政治、自然災害、働き方改革、第四次産業革命……。 不確実性が高まる環境変化の中にあって、日本の製造業には“企業変革力(ダイナミック・ケイパビリティ)”の強化が求められています。 そのためには、デジタル技術の徹底的な利活用が不可欠。データを収集しAIなどの技術を活用したデジタル・トランスフォーメーション(DX)の推進と、 3D設計やシミュレーションによる高速化などによる設計力強化が重要となります。
設計力を強化する戦略としては「フロントローディング」「エンジニアリングチェーンの強化」 「部門間のデータ連携」「バーチャル・エンジニアリング」の4点がキーポイントです。
全体最適を考慮したエンジニアリングチェーンの構築
NECでは、「ものづくりのプロセスで作り出されたデジタルデータで、社内外をつなぎ、 全体最適を考慮したエンジニアリングチェーンを構築すること」が、 設計力強化やデジタルエンジニアリングの実行に必要であると考えています。
営業、開発・設計、生産技術、資材調達、製造、品質保証、サービスなど多くの部門が関わるエンジニアリングチェーンは、 CADデータ管理PDMや情報共有基盤PLM、社外情報共有プラットフォームであらゆる情報を一貫性をもって集約管理することで形成できます。
これによってさまざまなデジタルデータを部門を超えて共有することで、コスト削減や品質向上、リードタイム短縮などの効果がもたらされるのです。
以下、デジタルデータやデジタル技術を活用したソリューションと事例をいくつかご紹介します。
Case1:PLM活用デジタルエンジニアリングの促進によるQCD向上
システム・データの分断により過去の設計資産を新製品の開発検討に活用できていませんでした。 そこで、設計力強化・設計資産の活用の軸となるPLMを再構築し、強固なエンジニアリングチェーンを形成。 活用できていなかった3D設計資産を、ものづくり工程の様々なフェーズで活用することで、 デジタルエンジニアリングの促進、QCD向上を実現しています。
Case2:工程情報BOPのデジタル化による原価精度・品質向上
品質管理の強化、トレーサビリティの向上、5M管理の強化、設備投資時の計画精度向上による収益改善といった4つの改革テーマに対して、 PLM「Obbligato(オブリガート)」導入により、BOM、工程情報、設備、金型、治工具などのリソース、それらに関連する成果物を統合管理しました。
それにより、原価企画、工程設計に必要な情報が素早く検索可能になり、これらの情報をグローバルレベルで管理することで、 工程企画時にグローバル拠点の設備情報を確認しながら、製造に最適な拠点の選定を可能としました。
また、各拠点で工程設計を行う際には、日本で設計した工程を流用してローカライズする方法をとったため、 拠点ごとに属人化せず、グローバルレベルで品質均一化を実現。もちろん海外含めてすべての情報の一貫性を持って管理しているため、 工程変更・設備不具合発生時にも、工程、製品含めた影響範囲を迅速に把握し、正しい情報をもとに、正確に対応できるようになりました。
Case3:3D類似形状検索による品質向上と永続的コスト削減
部品の整理が十分でなく、過去の製品や部品を検索するのに多大な工数をかけており、 検索性の低さにより、類似部品、互換可能な部品を新規に設計し管理維持コストが増大していました。
類似形状検索ソリューションの導入により、形状という新たな情報を基にした検索が可能となり、 検索性が大幅に向上、過去の設計資産をフルに活用し設計品質を向上しています。また、品質面の効果だけでなく、 設計工数の削減、部品標準化促進による金型コスト・管理維持コストの削減といった永続的なコスト削減も実現しています。
Case4:3Dデータの全社活用による設計品質向上、フロントローディングの促進
20年以上前から“設計の完全3D化”を目指し、解析シミュレーションなどを活用しながらフロントローディングを実践してきました。
そして、さらなるフロントローディングや品質向上のため、CADデータ管理PDMと全社情報共有基盤PLMを導入。
設計資産の連携自動化などにより、設計部門以外でデジタルデータを活用することによる開発リードタイム短縮、 設計仕掛段階から生産・サービスの作業着手など多くの効果を挙げています。
Case5:AR活用による製造・検査作業の効率化
AR(拡張現実)活用による製造・検査作業の効率化の事例です。
従来、2D図面や3D図面・モデルを必要分だけ用意して、図面上で、検査位置や製造作業位置を確認、 メジャーで位置を特定して、検査・製造といった流れで実施していた作業が、 ARソリューション「REFLEKT ONE(リフレクトワン)」の導入により、ARモデル上にあらかじめ検査位置や検査ポイント、 製造箇所の情報を集約・設定しておくことで、図面レス、測定での検査作業・製造作業が可能となり、 作業の効率化、作業工数の大幅削減に貢献しています。
Case6:工程設計情報のデジタル化・蓄積による生産全体の効率化
工程設計情報のデジタル化・蓄積による生産全体の効率化の事例です。
製品設計や生産においては、3DやBOM・BOPなどデジタルデータの活用が進んでいる一方、 生産準備フェーズでは現場での工程組替や机上での検討など、アナログな手法が多く残っています。
これによって多くの工数を費やすとともに、設計情報との不十分な連携で取りこぼしや重複など非効率の温床となっているほか、 現場の問題や改善結果が設計にフィードバックしづらい状況を生んでいました。
生産準備フェーズの業務改善のため、工程設計をデジタル化し、設計データから現場情報をデジタルで繋いで 開発・設計、生産準備、生産の全体を効率化するソリューションの開発を進めています。
以上のように、NECは、デジタルデータやデジタル技術を駆使し、製造業が直面する設計力強化などの課題解決施策を幅広くサポートしています。
また、当日はPLMソリューション「Obbligato(オブリガート)」・ARソリューション「REFLEKT ONE(リフレクトワン)」の動作動画のご紹介やQ&Aも実施され、 ご参加された皆さまにより具体的なイメージを持っていただけるよう、進行させていただきました。
ご参加いただいてこそ得られる情報も多数用意させていただいておりますので、これからのWebセミナーにもご注目いただけますと幸いです。
関連リンク
SOLIDWORKS デジタルものづくりを牽引する3DCAD
SOLIDWORKSは、革新的な機能と圧倒的な操作性で、優れたアイデアを実現するための最新で最高の設計環境を提供します。 また、設計業務の効率化を実現するとともに、設計初期段階から3DCADデータを他部門と共有することで、全社での活用を促進します。
お問い合わせ